Preparing method for alloy powder
A technology of alloy powder and alloy, which is applied in the field of preparation of alloy powder, to achieve the effect of easy operation, strong feasibility and application prospect, and simple process
- Summary
- Abstract
- Description
- Claims
- Application Information
AI Technical Summary
Problems solved by technology
Method used
Examples
preparation example Construction
[0033] The invention provides a preparation method of alloy powder, comprising the following steps:
[0034] (1) Under an inert atmosphere, the alkali metal salt or alkaline earth metal salt is heated to a molten state, and electrolysis is performed, and the following electrochemical reaction occurs on the cathode:
[0035] Me n+ + ne = Me (1)
[0036] Me n+ Alkali metal or alkaline earth metal ions, because the alkali metal or alkaline earth metal will dissolve in the electrolyte around the cathode to form an electrolyte containing metal mist. At this time, add an alloy-containing compound or an alloy-containing anode to the electrolyte around the cathode to decompose the alloy ions, the following reaction occurs:
[0037] Me+Me 1 n+ → Me n+ +Me 1 (2)
[0038] is reduced to the metal Me 1 The titanium alloy powder and the alloy element powder are alloyed in the electrolyte to obtain the corresponding titanium alloy powder. The alloy-containing compound is at least ...
Embodiment 1
[0041] Embodiment 1 adopts the method of the present invention to prepare titanium-aluminum alloy powder
[0042] Under the protection of argon atmosphere, the analytically pure NaCl-KCl electrolyte was heated to 850°C, a graphite anode and a steel cathode were inserted, and electrolysis was carried out by energizing. After 10 minutes of electrolysis, the molten salt in the cathode area was continuously fed with AlCl by using a quartz tube. 3 and TiCl 4 , the two are mixed in advance according to the molar ratio of 1:1, AlCl 3 and TiCl 4 The total amount of Na added is slightly less than the total amount of Na required for the stoichiometric ratio. After the electrolysis is completed, keep the temperature for 30 minutes. The electrolyte is cooled to below 100°C with the furnace. Titanium and aluminum ions that have not been reduced to simple substances, and then washed with water to AgNO 3 No chlorine ion was detected in the solution, it was filtered and air-dried at room t...
Embodiment 2
[0043] Example 2 Preparation of titanium-aluminum alloy powder by the method of the present invention
[0044]Under the protection of argon atmosphere, the analytically pure NaCl-KCl mixed salt is heated up to 700°C, a metal aluminum anode, a metal titanium anode and a steel cathode are inserted, and the electrolysis is carried out by energizing, and a current is energized on the two anodes They are 3A and 2A respectively. After 60 minutes of electrolysis, the electrolyte is cooled to below 100°C with the furnace, the electrolyte is chiseled out and broken, and the salt and unreduced titanium and aluminum ions are washed away with 0.2% hydrochloric acid, and then water Wash to AgNO 3 No chlorine ion was detected in the solution, it was filtered and air-dried at room temperature, and the O content was analyzed to be 1400PPm. The obtained titanium-aluminum alloy powder D of the present embodiment 50 It is 1.59um, Ti is 63.02% in chemical analysis alloy composition, and Al is 3...
PUM
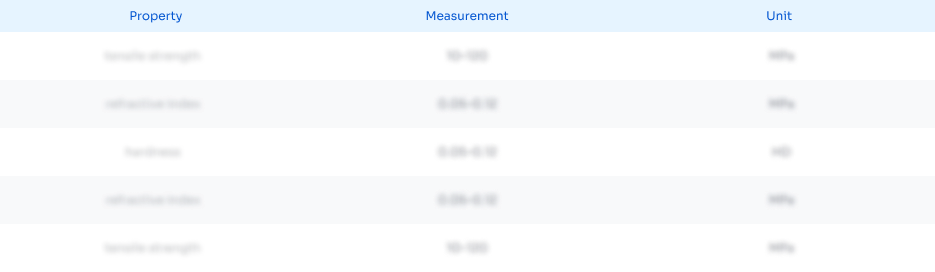
Abstract
Description
Claims
Application Information

- R&D Engineer
- R&D Manager
- IP Professional
- Industry Leading Data Capabilities
- Powerful AI technology
- Patent DNA Extraction
Browse by: Latest US Patents, China's latest patents, Technical Efficacy Thesaurus, Application Domain, Technology Topic, Popular Technical Reports.
© 2024 PatSnap. All rights reserved.Legal|Privacy policy|Modern Slavery Act Transparency Statement|Sitemap|About US| Contact US: help@patsnap.com