Zinc alloy for hot dip
A zinc alloy and hot-dip galvanizing technology, which is applied in the field of zinc alloy for hot-dip galvanizing, can solve the problems that zinc alloy cannot be applied to hot-dip, the increase of zinc alloy liquid iron particles, and zinc waste, so as to solve the problem of poor coating adhesion and reduce raw material cost, and the effect of reducing the generation of bottom dross
- Summary
- Abstract
- Description
- Claims
- Application Information
AI Technical Summary
Problems solved by technology
Method used
Examples
Embodiment 1
[0017] A zinc alloy S1 for hot dipping, its composition is 20.0wt% Al, 0.1wt% Ni, 0.1wt% Mn, 0.05wt% Sn, 0.05wt% Cr, 0.01wt% RE (LaCe mixed) , and the balance is unavoidable impurities brought by Zn and zinc alloys.
[0018] Using the zinc alloy S1 for hot dipping in this example to hot-dip steel pipes for 1.5 minutes, the thickness of the formed coating is uniform, and the thickness distribution of the coating is 50-70 μm. Monthly hot-dip galvanized alloy liquid iron content maintained at 0.0083%.
Embodiment 2
[0020] A zinc alloy S2 for hot dipping, its composition is 0.2wt% Al, 0.1wt% Ni, 0.1wt% Mn, 0.05wt% Sn, 0.05wt% Cr, 0.15wt% RE (LaCe mixed) , and the balance is unavoidable impurities brought by Zn and zinc alloys.
[0021] Adopt zinc alloy S2 for hot dipping of this embodiment to hot-dip galvanize strip steel for 15 seconds, the thickness of the formed coating is uniform, and the thickness distribution of the coating is 10-30 μm, the adhesion test is good, the coating is bright and clean, and there is very little bottoming. Slag, half a month hot-dip galvanized alloy liquid iron content maintained at 0.0014%.
Embodiment 3
[0023] A zinc alloy S3 for hot dipping, its composition is 5wt% Al, 0.2wt% Ni, 0.3wt% Mn, 0.2wt% Sn, 0.1wt% Cr, 0.05wt% RE (LaCe mixed), The balance is unavoidable impurities contained in Zn and zinc alloys.
[0024] Adopt zinc alloy S3 for hot-dipping of the present embodiment to hot-dip 3 minutes on the high-silicon high-manganese steel big tube tower piece with disk at both ends, the coating thickness that forms is uniform, and coating thickness distribution is 85-115 μ m, adhesion force The test is good, the coating is bright and clean, very little bottom dross is produced, and the iron content of the hot-dip galvanized alloy liquid is maintained at 0.0056% for half a month.
PUM
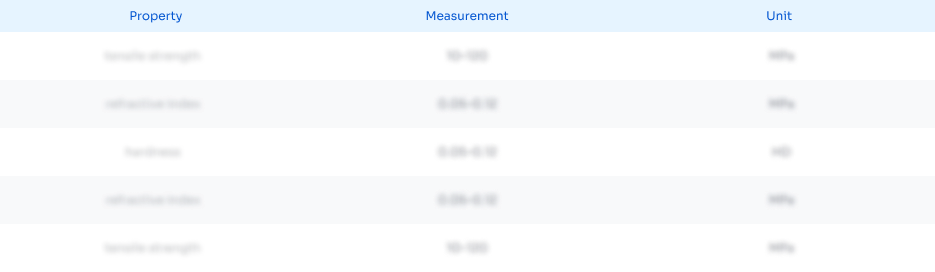
Abstract
Description
Claims
Application Information

- R&D Engineer
- R&D Manager
- IP Professional
- Industry Leading Data Capabilities
- Powerful AI technology
- Patent DNA Extraction
Browse by: Latest US Patents, China's latest patents, Technical Efficacy Thesaurus, Application Domain, Technology Topic, Popular Technical Reports.
© 2024 PatSnap. All rights reserved.Legal|Privacy policy|Modern Slavery Act Transparency Statement|Sitemap|About US| Contact US: help@patsnap.com