Secondary aluminum melting process
A recycled aluminum and process technology, which is applied in the direction of improving process efficiency, can solve the problems such as poor processing effect of recycled aluminum, and achieve the effects of improving mechanical properties and corrosion resistance, enhancing mechanical strength, and reducing deformation
- Summary
- Abstract
- Description
- Claims
- Application Information
AI Technical Summary
Problems solved by technology
Method used
Examples
Embodiment 1
[0040] Use cleaning solution to clean new and recycled materials; break waste cans into 1cm-long strips of aluminum, and then pass through a wind separator for the first separation under the condition of a wind speed of 4m / s to separate light Impurities. Then, through a magnetic separator, the second separation is carried out under the condition of a magnetic field strength of 0.1T, and the iron filings are separated. Next, put the aluminum strip into 15% acetic acid solution for immersion for 3 minutes, then heat the aluminum strip to 80° C. and perform mechanical kneading.
[0041] Add the rubbed aluminum strip while hot to the first mixture of benzyl alcohol, acetic acid and turpentine with a volume ratio of 3:1:1 and stir for 15 minutes, then put in the second mixture of 4:1 absolute ethanol and ethyl acetate. The mixture was stirred for 10 minutes, ultrasonically oscillated in deionized water for 30 minutes, and then dried at 110°C for 20 minutes.
[0042] Then batching i...
Embodiment 2
[0050] Use cleaning solution to clean new and recycled materials; break waste cans into 1cm-long strips of aluminum, and then pass through a wind separator for the first separation under the condition of a wind speed of 4m / s to separate light Impurities. Then, through a magnetic separator, the second separation is carried out under the condition of a magnetic field strength of 0.1T, and the iron filings are separated. Next, put the aluminum strip into 15% acetic acid solution for immersion for 3 minutes, then heat the aluminum strip to 80° C. and perform mechanical kneading.
[0051] Add the rubbed aluminum strip while hot to the first mixture of benzyl alcohol, acetic acid and turpentine with a volume ratio of 3:1:1 and stir for 15 minutes, then put in the second mixture of 4:1 absolute ethanol and ethyl acetate. The mixture was stirred for 10 minutes, ultrasonically oscillated in deionized water for 30 minutes, and then dried at 110°C for 20 minutes.
[0052] Then batching...
Embodiment 3
[0057] Use cleaning solution to clean new and recycled materials; break waste cans into 1cm-long strips of aluminum, and then pass through a wind separator for the first separation under the condition of a wind speed of 4m / s to separate light Impurities. Then, through a magnetic separator, the second separation is carried out under the condition of a magnetic field strength of 0.1T, and the iron filings are separated. Next, put the aluminum strip into 15% acetic acid solution for immersion for 3 minutes, then heat the aluminum strip to 80° C. and perform mechanical kneading.
[0058] Add the rubbed aluminum strip while hot to the first mixture of benzyl alcohol, acetic acid and turpentine with a volume ratio of 3:1:1 and stir for 15 minutes, then put in the second mixture of 4:1 absolute ethanol and ethyl acetate. The mixture was stirred for 10 minutes, ultrasonically oscillated in deionized water for 30 minutes, and then dried at 110°C for 20 minutes.
[0059] Then carry ou...
PUM
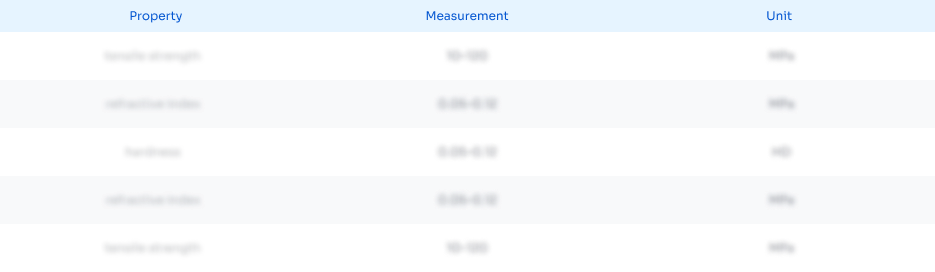
Abstract
Description
Claims
Application Information

- R&D Engineer
- R&D Manager
- IP Professional
- Industry Leading Data Capabilities
- Powerful AI technology
- Patent DNA Extraction
Browse by: Latest US Patents, China's latest patents, Technical Efficacy Thesaurus, Application Domain, Technology Topic, Popular Technical Reports.
© 2024 PatSnap. All rights reserved.Legal|Privacy policy|Modern Slavery Act Transparency Statement|Sitemap|About US| Contact US: help@patsnap.com