Extrusion-molding method solvent-free waterborne polyurethane dispersion as well as preparation method and application thereof
A water-based polyurethane, solvent-free technology, applied in the field of extrusion solvent-free water-based polyurethane dispersion and its preparation and application, can solve the problem of not involving urea-based structural reaction, unable to truly prepare water-based polyurethane dispersion, and the molecular weight of water-based polyurethane dispersion. problems such as small solvents, to achieve the effect of improving cohesive energy, low implementation cost, and improving performance
- Summary
- Abstract
- Description
- Claims
- Application Information
AI Technical Summary
Problems solved by technology
Method used
Image
Examples
Embodiment 1
[0046] Formula: (mass percentage)
[0047]
[0048] Preparation:
[0049] (1) Mix and heat polytetrahydrofuran diol (Mn=2000), dimethylol butyric acid, and 1,4-butanediol to 80°C, add catalyst stannous octoate, 4,4-diphenylmethane diisocyanate ( MDI) is heated up to 80°C, the above two are respectively passed through the gear metering pump, the flow meter, and the injection speed after passing through the mixing head is 250rpm, L / D=45, and the temperature is 120°C, 130°C, 140°C, 150°C, 150°C °C, 160 °C, 210 °C twin-screw reactor reaction, the residence time is 0.5min;
[0050] (2) Injection temperature is 150 ℃, rotating speed is 1500rpm in the shear pump through melt gear pump, simultaneously temperature is 150 ℃, pressure is 0.5Mpa and concentration is that 2.6%wt triethylamine aqueous solution also injects in the shear pump, shears 4min;
[0051] (3) Cool down to 30°C through a heat exchanger, reduce the pressure to normal pressure, and collect it in a stainless steel...
Embodiment 2
[0053] Formula: (mass percentage)
[0054]
[0055]
[0056] Preparation:
[0057] (1) Mix and heat 1,4-butanediol polyadipate (Mn=2000), dimethylol butyric acid, and 1,4-butanediol to 100°C, add the catalyst stannous octoate, and hydrogenate The temperature of 4,4-diphenylmethane diisocyanate (HMDI) is raised to 100°C, and the above two materials pass through the gear metering pump and the flow meter respectively, and then the injection speed is 250rpm, L / D=30, and the temperature is 120°C, 120°C, 130°C, 140°C, 150°C, 170°C, 215°C twin-screw reactor reaction, the residence time is 2min;
[0058] (2) Injection temperature is 100 DEG C, rotating speed is in the shear pump of 1000rpm through melt gear pump, simultaneously temperature is 100 DEG C, pressure is 0.2Mpa, concentration is that 2.3%wt methyldiethanolamine aqueous solution also injects in shear pump, Cut for 5 minutes;
[0059] (3) The temperature is lowered to 50°C by a heat exchanger, the pressure is lowered...
Embodiment 3
[0061] Formula: (mass percentage)
[0062]
[0063] Preparation:
[0064] (1) Polytetrahydrofuran diol (Mn=2000), poly-1,4-butylene adipate diol (Mn=2000), dimethylol butyric acid, 2-methyl-1,3- Propylene glycol is mixed and heated to 60°C, the catalyst stannous octoate is added, and the temperature of hydrogenated 4,4-diphenylmethane diisocyanate (HMDI) is raised to 60°C. The above two are injected through the gear metering pump and flow meter respectively, and the speed of injection after passing through the mixing head is 200rpm, L / D=56, twin-screw reactor reaction at temperatures of 80°C, 100°C, 130°C, 140°C, 150°C, 170°C, and 215°C, and the residence time is 1min;
[0065] (2) Inject the melt gear pump into the shear pump with a temperature of 200°C and a rotational speed of 2500rpm. At the same time, the temperature is 200°C and the pressure is 0.2Mpa. The aqueous solution of triethanolamine with a concentration of 3.1%wt is also injected into the shear pump and shea...
PUM
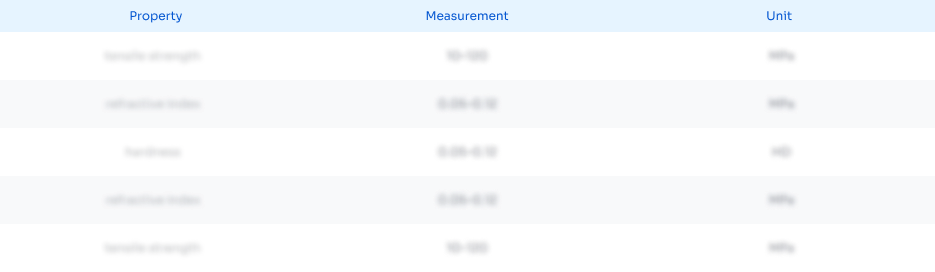
Abstract
Description
Claims
Application Information

- R&D
- Intellectual Property
- Life Sciences
- Materials
- Tech Scout
- Unparalleled Data Quality
- Higher Quality Content
- 60% Fewer Hallucinations
Browse by: Latest US Patents, China's latest patents, Technical Efficacy Thesaurus, Application Domain, Technology Topic, Popular Technical Reports.
© 2025 PatSnap. All rights reserved.Legal|Privacy policy|Modern Slavery Act Transparency Statement|Sitemap|About US| Contact US: help@patsnap.com