Radiant tube of quick pyrolyzing furnace without heat carriers
A radiant tube and pyrolysis furnace technology, applied in the field of gas-fired radiant tubes, can solve the problems of reduced heat transfer efficiency, easy material accumulation, and large material obstruction effect, so as to achieve the advantages of increasing the area, increasing the heat transfer area, and increasing the effect of distribution. Effect
- Summary
- Abstract
- Description
- Claims
- Application Information
AI Technical Summary
Problems solved by technology
Method used
Image
Examples
Embodiment 1
[0039] The radiant tubes of the present invention are staggeredly arranged in the hearth of an experimental furnace, and the experiment of coal powder particles is carried out on the experimental furnace.
[0040] The uniformity of the cloth is measured by measuring the height of the falling material layer, the particle size is 1mm, and the particle bulk density is 1.0kg / cm 3 , r=25mm, R=100mm, h=180mm (h is the distance between the upper and lower fan-shaped centers), the experimental results are as follows: the material accumulation height at the upper end of the radiant tube is much smaller than that of the ordinary radiant tube, and the maximum thickness of the blanking layer is higher than the minimum thickness High 3 ~ 5%, basically achieve uniform cloth.
[0041] In summary, the reduced upper section of the radiant tube of the present invention reduces the hindrance of the radiant tube to the falling materials, which can better increase the cloth distribution effect an...
PUM
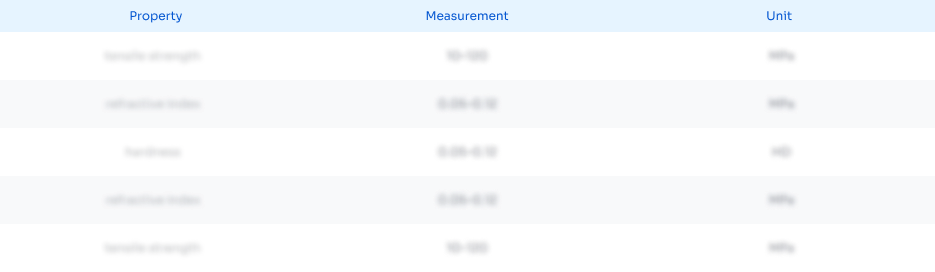
Abstract
Description
Claims
Application Information

- R&D
- Intellectual Property
- Life Sciences
- Materials
- Tech Scout
- Unparalleled Data Quality
- Higher Quality Content
- 60% Fewer Hallucinations
Browse by: Latest US Patents, China's latest patents, Technical Efficacy Thesaurus, Application Domain, Technology Topic, Popular Technical Reports.
© 2025 PatSnap. All rights reserved.Legal|Privacy policy|Modern Slavery Act Transparency Statement|Sitemap|About US| Contact US: help@patsnap.com