Manufacturing method for super-barrier hollow container
A container manufacturing and hollowing technology, which is applied in the field of ultra-barrier multi-layer hollow container manufacturing, can solve the problems of poor organic solvent barrier, shortened container service life, difficult drop function, etc., to achieve high impact resistance, improved production efficiency, shortened The effect of the production cycle
- Summary
- Abstract
- Description
- Claims
- Application Information
AI Technical Summary
Problems solved by technology
Method used
Examples
Embodiment
[0016] A specific implementation of a method for manufacturing a super-barrier multi-layer hollow container, including: a blow molding process, a preform made of resin material in the extrusion blow mold, the resin material includes polyethylene (abbreviated as "PE") ") and polyethylene terephthalate (abbreviated as "PET"), and barrier materials composed of nylon (abbreviated as "PA") and polyvinyl alcohol (abbreviated as "EVON"), in T1 Blow nitrogen gas from one end of the preformed embryo into the embryo with the first air pressure P1 within a certain period of time to form a hollow embryo body with a first volume. When the air pressure reaches P1, hold the pressure for T2 time. If the air pressure does not reach The first air pressure P1 will trigger the low pressure sensor alarm device to indicate insufficient pressure; in the mixed blow molding process, reduce P1 to the second air pressure P2 within T3 time, otherwise the high pressure sensor alarm device will be triggered...
PUM
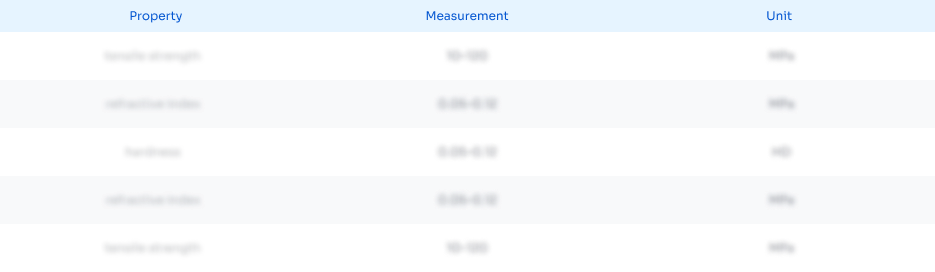
Abstract
Description
Claims
Application Information

- R&D
- Intellectual Property
- Life Sciences
- Materials
- Tech Scout
- Unparalleled Data Quality
- Higher Quality Content
- 60% Fewer Hallucinations
Browse by: Latest US Patents, China's latest patents, Technical Efficacy Thesaurus, Application Domain, Technology Topic, Popular Technical Reports.
© 2025 PatSnap. All rights reserved.Legal|Privacy policy|Modern Slavery Act Transparency Statement|Sitemap|About US| Contact US: help@patsnap.com