Preparation method of polyurethane sieve plate
A technology of polyurethane and sieve plate, applied in the field of polyurethane sieve plate, can solve the problems of poor strength and wear resistance, poor adaptability, easy hydrolysis and other problems, and achieve the effect of improving hydrolysis resistance, improving wear resistance and improving water resistance
- Summary
- Abstract
- Description
- Claims
- Application Information
AI Technical Summary
Problems solved by technology
Method used
Image
Examples
Embodiment 1
[0020] A preparation method of polyurethane sieve plate, comprising the following steps:
[0021] (1) Preparation of prepolymer: uniformly mix polycaprolactone polyol, polytetrahydrofuran, silicon deposition modified nano-alumina, coupling agent, sodium dodecylbenzene sulfonate, add to the reaction kettle, heat To 80°C, stir at 2500r / min for 40min, then raise the temperature of the reactor to 112°C, adjust the pressure inside the reactor to 0.04MPa, keep the temperature and pressure and stir for 1.5h, then pass helium into the reactor to remove the air , then add diphenylmethane diisocyanate, adjust the temperature to 102°C, and react for 2.5h to obtain a modified polyurethane prepolymer; the mass ratio of polycaprolactone polyol to polytetrahydrofuran is 1:5.1; The amount of silicon deposition modified nano-alumina added is 20% of the quality of polytetrahydrofuran; the quality of the coupling agent is 0.15% of the quality of silicon deposition modified nano-alumina; the qual...
Embodiment 2
[0034] A preparation method of polyurethane sieve plate, comprising the following steps:
[0035] (1) Preparation of prepolymer: uniformly mix polycaprolactone polyol, polytetrahydrofuran, silicon deposition modified nano-alumina, coupling agent, sodium dodecylbenzene sulfonate, add to the reaction kettle, heat To 90°C, stir at 2500r / min for 40min, then raise the temperature of the reactor to 115°C, adjust the pressure inside the reactor to 0.06MPa, keep the temperature and pressure and stir for 1.5h, then pass helium into the reactor to remove the air , then add diphenylmethane diisocyanate, adjust the temperature to 102°C, and react for 2.5h to obtain a modified polyurethane prepolymer; the mass ratio of polycaprolactone polyol to polytetrahydrofuran is 1: 5.5; The amount of silicon deposition modified nano-alumina added is 20% of the quality of polytetrahydrofuran; the quality of the coupling agent is 0.15% of the quality of silicon deposition modified nano-alumina; the qua...
Embodiment 3
[0048] A preparation method of polyurethane sieve plate, comprising the following steps:
[0049] (1) Preparation of prepolymer: uniformly mix polycaprolactone polyol, polytetrahydrofuran, silicon deposition modified nano-alumina, coupling agent, sodium dodecylbenzene sulfonate, add to the reaction kettle, heat To 85°C, stir at 2500r / min for 40min, then raise the temperature of the reactor to 113°C, adjust the pressure inside the reactor to 0.05MPa, keep the temperature and pressure and stir for 1.5h, then pass helium into the reactor to remove the air , then add diphenylmethane diisocyanate, adjust the temperature to 102°C, and react for 2.5h to obtain a modified polyurethane prepolymer; the mass ratio of polycaprolactone polyol to polytetrahydrofuran is 1:5.3; The amount of silicon deposition modified nano-alumina added is 20% of the quality of polytetrahydrofuran; the quality of the coupling agent is 0.15% of the quality of silicon deposition modified nano-alumina; the qual...
PUM
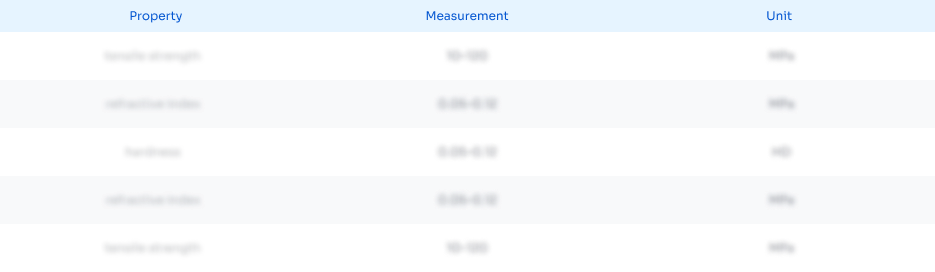
Abstract
Description
Claims
Application Information

- R&D
- Intellectual Property
- Life Sciences
- Materials
- Tech Scout
- Unparalleled Data Quality
- Higher Quality Content
- 60% Fewer Hallucinations
Browse by: Latest US Patents, China's latest patents, Technical Efficacy Thesaurus, Application Domain, Technology Topic, Popular Technical Reports.
© 2025 PatSnap. All rights reserved.Legal|Privacy policy|Modern Slavery Act Transparency Statement|Sitemap|About US| Contact US: help@patsnap.com