Preparation method of low-temperature sintered electronic ceramic material
A low-temperature sintering technology for electronic ceramics, applied in the field of electronic ceramic materials, can solve the problems of inability to use conductive metals, etc., and achieve the effects of reducing production costs, simple formula, and reducing the content of impurities
- Summary
- Abstract
- Description
- Claims
- Application Information
AI Technical Summary
Problems solved by technology
Method used
Image
Examples
preparation example Construction
[0022] refer to Figure 1-2 , a preparation method of low-temperature sintered electronic ceramic material, comprising the following steps:
[0023] The first step: mix various preparation raw materials in proportion, grind the raw materials and add them to the solvent, prepare a suspension by adding a suspending agent, pass through the casting nozzle, and the suspension slurry flows to the steadily rotating endless steel belt by its own weight, and passes through The raw material film is obtained by drying in multiple cycles.
[0024] Step 2: add binder and plasticizer to the raw material film, mix and grind once through a ball mill to get the mixture powder, put the mixture powder into the drying box, and stay between 80°C and 120°C for six to twelve Hours, drying and drying.
[0025] Step 3: Put the dried mixture powder into the pre-sintering furnace for pre-sintering treatment, put the dried mixture powder into the pre-sintering furnace, adjust the pre-sintering furnace ...
Embodiment 1
[0033] A method for preparing a low-temperature sintered electronic ceramic material. The raw materials for the preparation include the following materials in parts by weight: 20 parts of titanium oxide, 10 parts of zirconium silicate, 4 parts of calcium oxide, 5 parts of nickel oxide, 5 parts of copper oxide, magnesium titanate 3 parts, 15 parts of iron oxide and 15 parts of zinc oxide are mixed.
Embodiment 2
[0035] A method for preparing a low-temperature sintered electronic ceramic material. The raw materials for the preparation include the following materials in parts by weight: 25 parts of titanium oxide, 15 parts of zirconium silicate, 8 parts of calcium oxide, 7 parts of nickel oxide, 8 parts of copper oxide, magnesium titanate 6 parts, 17 parts of iron oxide and 18 parts of zinc oxide are mixed.
PUM
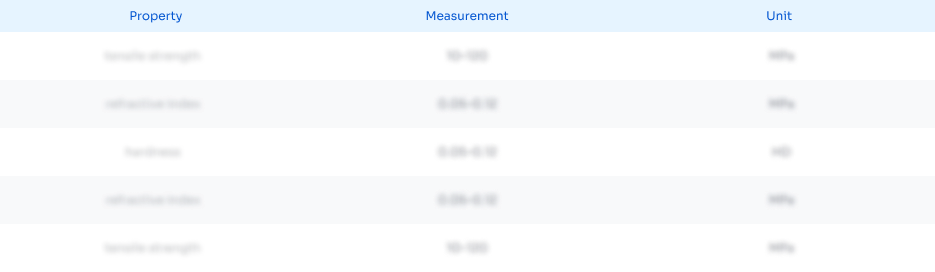
Abstract
Description
Claims
Application Information

- R&D Engineer
- R&D Manager
- IP Professional
- Industry Leading Data Capabilities
- Powerful AI technology
- Patent DNA Extraction
Browse by: Latest US Patents, China's latest patents, Technical Efficacy Thesaurus, Application Domain, Technology Topic, Popular Technical Reports.
© 2024 PatSnap. All rights reserved.Legal|Privacy policy|Modern Slavery Act Transparency Statement|Sitemap|About US| Contact US: help@patsnap.com