Superfine cobalt powder preparation method
A technology of ultra-fine cobalt powder and cobalt powder, which is applied in metal processing equipment, transportation and packaging, etc., can solve the problems of complicated process and equipment, increase production cost, etc., and achieve the effects of stable product quality, improved production efficiency and simple operation.
- Summary
- Abstract
- Description
- Claims
- Application Information
AI Technical Summary
Problems solved by technology
Method used
Image
Examples
Embodiment 1
[0020] (1) 3.0 kg of spherical cobalt carbonate of 0.7 μm is loaded into each boat and placed in a tube furnace, and the N 2 The flow rate is 4.0m 3 / h, the thermal decomposition temperature is 400°C, the time is 6 hours, and the cobaltous oxide powder is produced;
[0021] (2) The cobaltous oxide powder obtained in step (1) is placed in a hydrogen reduction furnace, and H in the reducing gas 2 :N 2 :H 2 The volume ratio of O is 3:1:0.01, and the control gas flow rate is 6.0m 3 / h, the reduction temperature is 450°C, and the reduction time is 8 hours, and finally a spherical ultrafine cobalt powder is obtained, with an average particle size of 0.6 μm.
[0022] Figure 1 ~ Figure 3 The photos of the superfine cobalt powder produced in this embodiment under the s4800 type field emission scanning electron microscope are 1000 times, 2000 times and 5000 times respectively, and we can see that its crystal form is a spherical shape.
Embodiment 2
[0024] (1) 2.0 kg of 0.5 μm spherical cobalt carbonate is loaded into each boat and placed in a tube furnace to control CO 2 The flow rate is 6.0m 3 / h, the thermal decomposition temperature is 300°C, the time is 8 hours, and the cobaltous oxide powder is produced;
[0025] (2) The cobaltous oxide powder obtained in step (1) is placed in a hydrogen reduction furnace, and H in the reducing gas 2 :N 2 :H 2 The volume ratio of O is 3:1:0.02, and the control gas flow rate is 4.0m 3 / h, the reduction temperature is 350°C, and the reduction time is 10 hours, and finally a spherical ultrafine cobalt powder is obtained, with an average particle size of 0.4 μm.
Embodiment 3
[0027] (1) 4.0kg of 1.0μm spherical cobalt carbonate is loaded into each boat and placed in a tube furnace, and the Ar flow rate is controlled to be 2.0m 3 / h, the thermal decomposition temperature is 600°C, the time is 4 hours, and the cobaltous oxide powder is produced;
[0028] (2) The cobaltous oxide powder obtained in step (1) is placed in a hydrogen reduction furnace, and H in the reducing gas 2 :N 2 :H 2 The volume ratio of O is 3:1:0.01, and the control gas flow rate is 8.0m 3 / h, the reduction temperature is 500°C, and the reduction time is 6 hours, and finally a spherical ultrafine cobalt powder is obtained, with an average particle size of 1.0 μm.
[0029] In summary, the present invention adopts the two-step method of decomposition and reduction to control the particle size and morphology of cobalt powder, and decomposes ultrafine cobalt carbonate in an inert gas atmosphere to obtain a single cobaltous oxide powder. It can be quickly reduced to cobalt powder. T...
PUM
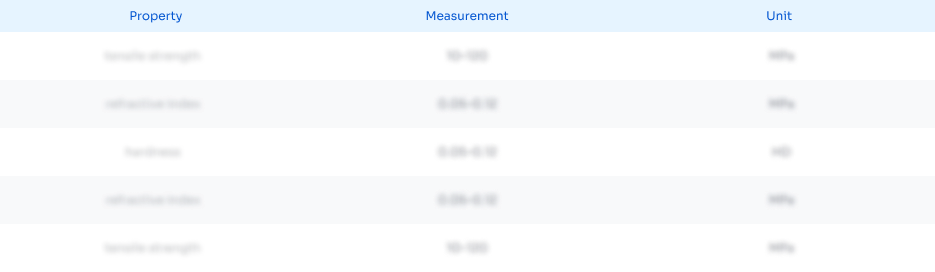
Abstract
Description
Claims
Application Information

- R&D Engineer
- R&D Manager
- IP Professional
- Industry Leading Data Capabilities
- Powerful AI technology
- Patent DNA Extraction
Browse by: Latest US Patents, China's latest patents, Technical Efficacy Thesaurus, Application Domain, Technology Topic, Popular Technical Reports.
© 2024 PatSnap. All rights reserved.Legal|Privacy policy|Modern Slavery Act Transparency Statement|Sitemap|About US| Contact US: help@patsnap.com