Method for producing nitroalkane and co-producing ketoxime
A technology of nitroalkane and nitropropane, which is applied in the field of producing nitroalkane and co-producing ketoxime, can solve the problems that do not involve high-selectivity nitroalkane and co-produce ketoxime, and achieve high product yield and process reaction The effect of mild conditions and enhanced production flexibility
- Summary
- Abstract
- Description
- Claims
- Application Information
AI Technical Summary
Problems solved by technology
Method used
Image
Examples
Embodiment 1
[0041] A 500mL three-necked glass flask was used as a reactor, and 10g of Ti-MWW molecular sieve catalyst, 50g of tert-butanol, 50g of water and 38g of acetone were sequentially added to it, and a magnetic stirrer made of polytetrafluoroethylene was placed in the flask. The interface in the middle of the flask is connected to the reflux of the condensing tube, and the ports on both sides are pumped into 135g of 25% ammonia (45g / hour) and 87g of 33% aqueous hydrogen peroxide (29g / hour) with a peristaltic pump in 3 hours. ). The reaction temperature is set at 60° C., the magnetic stirring is at 160 rpm, and the reaction pressure is at 0.1 MPa. After the feeding of ammonia water and hydrogen peroxide aqueous solution was completed, the reaction conditions were maintained to continue the reaction for 2 hours.
[0042] The reaction result is that the conversion rate of acetone is about 99%, the selectivity of 2-nitropropane is about 25%, and the selectivity of acetone oxime is abo...
Embodiment 2
[0045] A 500mL three-necked glass flask was used as a reactor, and 15g of TS-1 molecular sieve catalyst, 100g of water and 38g of acetone were sequentially added into it, and a magnetic stirring bar made of polytetrafluoroethylene was placed in the flask. The middle interface of the flask is connected to the reflux of the condenser tube, and 26L of ammonia gas (87 ml / min rate) and 120g of 33% ammonia gas (at a rate of 87 ml / min) are introduced into the interface on both sides within 5 hours under the control of a gas mass flow meter and a peristaltic pump is used within 5 hours. Aqueous hydrogen peroxide solution (24 g / hour rate). The reaction temperature was set at 68° C., the magnetic stirring was at 160 rpm, and the reaction pressure was 0.1 MPa. After the feeding of ammonia and aqueous hydrogen peroxide solution was completed, the reaction conditions were maintained for 2 hours.
[0046] The reaction result is that the conversion rate of acetone is about 98%, the selectiv...
Embodiment 3
[0049] A 500mL stainless steel reactor was used as the reactor, and 5g of Ti-HMS molecular sieve catalyst and 5g of TS-1 molecular sieve catalyst, 100g of isopropanol and 38g of acetone were sequentially added into it, and the materials were mixed with a mechanical stirring paddle. Add 89g concentration of 25% ammoniacal liquor at one time, then pass into 120g concentration 25% hydrogen peroxide aqueous solution (15g / hour speed) in 8 hours with high-pressure advection pump then. The reaction temperature was set at 55° C., the stirring blade was set at 160 rpm, and the reaction pressure was 0.5 MPa. After the aqueous hydrogen peroxide solution was fed, the reaction conditions were maintained to continue the reaction for 2 hours.
[0050] The reaction result is that the conversion rate of acetone is about 100%, the selectivity of 2-nitropropane is about 15.5%, and the selectivity of acetone oxime is about 80.5%.
[0051] The treatment of the reacted material was then the same ...
PUM
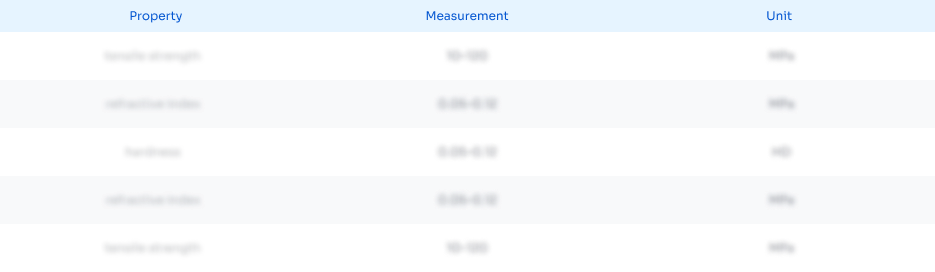
Abstract
Description
Claims
Application Information

- R&D
- Intellectual Property
- Life Sciences
- Materials
- Tech Scout
- Unparalleled Data Quality
- Higher Quality Content
- 60% Fewer Hallucinations
Browse by: Latest US Patents, China's latest patents, Technical Efficacy Thesaurus, Application Domain, Technology Topic, Popular Technical Reports.
© 2025 PatSnap. All rights reserved.Legal|Privacy policy|Modern Slavery Act Transparency Statement|Sitemap|About US| Contact US: help@patsnap.com