Refining method for molten steel
A technology of molten steel and refining slag, applied in the field of iron and steel smelting, can solve the problems of hard slag, insufficient adsorption capacity of inclusions, high FeO content, etc., achieve the effect of reducing inclusion defects and improving the capacity of slag to absorb inclusions
- Summary
- Abstract
- Description
- Claims
- Application Information
AI Technical Summary
Problems solved by technology
Method used
Examples
Embodiment 1
[0063] Ultra-low carbon automotive panel DC06 steel produced by Pangang Group Xichang Steel and Vanadium Co., Ltd. The production process is converter-LF-RH-casting machine.
[0064] DC06 is the production furnace of automobile panel steel. During the tapping process, 500kg of active lime is added to each furnace. After the converter is tapped, the molten steel is hoisted to LF for processing. During the LF heating process, 15-20kg / t of tailing slag for making alloys is added, and 500-1500kg / furnace of active lime is added during the treatment process for submerged arc heating to prevent nitrogen increase. Using SiO in ladle slag 2 , FeO and Al in tailings 2 o 3 To carry out the reaction, the electric arc in the heating process promotes the dissolution of the tailings, and produces a slag phase with a low melting point and an appropriate proportion of members. Usually, in order to ensure a reasonable slag phase, when 600kg of lime is added, the amount of tailings should be...
Embodiment 2
[0067] Low-carbon aluminum DC01 steel for home appliances produced by Pansteel Group Xichang Steel and Vanadium Co., Ltd. The production process is converter-RH-casting machine.
[0068] DC01 home appliance plate steel production furnace, adding active lime 500kg / furnace during the tapping process, adding 300kg tailing slag for making alloys during the tapping process, using SiO2, FeO in the ladle slag and Al in the tailing slag 2 o 3 Carry out the reaction, use the heat flow stirring in the tapping process to promote the dissolution of tailing slag, produce a slag phase with a low melting point and a suitable ratio of members, add a modifier containing aluminum balls to the ladle after tapping to deoxidize the slag, and the dosage is 200kg / furnace. Usually, the proportion of lime and tailings is controlled in the range of 3:1 to 2:1 to ensure that the CaO content in the slag is controlled at 30% to 45%, and the Al 2 o 3 Controlled at 20-35%, the formed 12(CaO)·7(Al 2 o ...
PUM
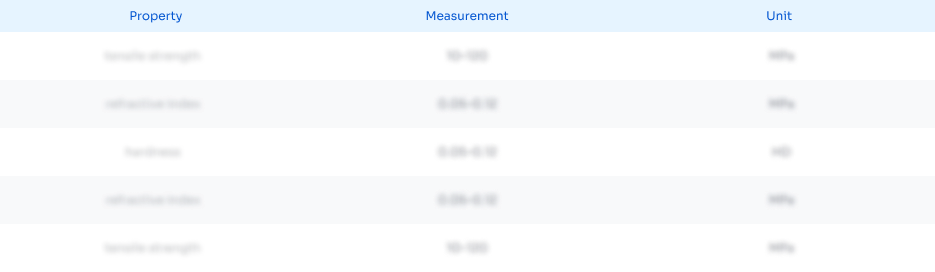
Abstract
Description
Claims
Application Information

- R&D Engineer
- R&D Manager
- IP Professional
- Industry Leading Data Capabilities
- Powerful AI technology
- Patent DNA Extraction
Browse by: Latest US Patents, China's latest patents, Technical Efficacy Thesaurus, Application Domain, Technology Topic, Popular Technical Reports.
© 2024 PatSnap. All rights reserved.Legal|Privacy policy|Modern Slavery Act Transparency Statement|Sitemap|About US| Contact US: help@patsnap.com