Phosphating solution for electrophoresis and preparation method thereof
A phosphating solution and electrophoresis technology, applied in electrophoretic plating, electrolytic coatings, metal material coating processes, etc., can solve the problems of uneven coating layer, corrosion, poor alkali resistance, etc., to achieve uniform phosphating coating layer, Effects of improved corrosion resistance and improved alkali resistance
- Summary
- Abstract
- Description
- Claims
- Application Information
AI Technical Summary
Problems solved by technology
Method used
Image
Examples
Embodiment 1
[0025] Premixing: Take 35kg of zinc oxide, 225kg of phosphoric acid, 16kg of magnesium stearate, 15kg of polyoxyethylene sorbitan laurate, and 380kg of water and stir until dissolved to obtain a premixed solution. The premixed temperature is 45°C and the stirring time is 15min;
[0026] Mixing: Add 35 kg of manganese dihydrogen phosphate, 5 kg of tartaric acid, 10 kg of hydrochloric acid, and 23 kg of sodium nitrite to the premixed solution, and stir evenly until the reaction is complete to obtain a phosphating solution. The mixing temperature is 37°C and the stirring time is 25 minutes;
[0027] Wherein, the concentration of phosphoric acid is 0.8g / L, the concentration of tartaric acid is 0.2g / L, and the concentration of hydrochloric acid is 0.3g / L.
Embodiment 2
[0029] Premixing: Take 30kg of zinc dihydrogen phosphate, 210kg of phosphoric acid, 13kg of aluminum stearate, 15kg of polyoxyethylene sorbitan laurate, 12kg of ethylene glycol stearate, and 400kg of water and stir until dissolved , to obtain a premix solution, wherein the premix temperature is 48°C, and the stirring time is 10min;
[0030] Mixing: Add 35kg of manganese hypophosphite, 7kg of tartaric acid, 6kg of hydrochloric acid, and 20kg of potassium nitrite to the premixed solution, and stir evenly until the reaction is complete to obtain a phosphating solution, wherein the mixing temperature is 35°C and the stirring time is 20 minutes;
[0031] Wherein, the concentration of phosphoric acid is 0.8g / L, the concentration of tartaric acid is 0.2g / L, and the concentration of hydrochloric acid is 0.3g / L.
Embodiment 3
[0033] Premixing: Take 30kg of zinc dithiophosphate, 240kg of phosphoric acid, 13kg of magnesium stearate, 12kg of polyoxyethylene sorbitan laurate, and 400kg of water and stir until dissolved to obtain a premixed liquid, wherein the premixed temperature is 42°C. Stirring time is 20min;
[0034] Mixing: Add 40kg of manganese carbonate, 7kg of tartaric acid, 6kg of hydrochloric acid, and 26kg of potassium nitrite to the premixed solution, and stir evenly until the reaction is complete to obtain a phosphating solution. The mixing temperature is 35°C and the stirring time is 20 minutes;
[0035] Wherein, the concentration of phosphoric acid is 0.8g / L, the concentration of tartaric acid is 0.2g / L, and the concentration of hydrochloric acid is 0.3g / L.
PUM
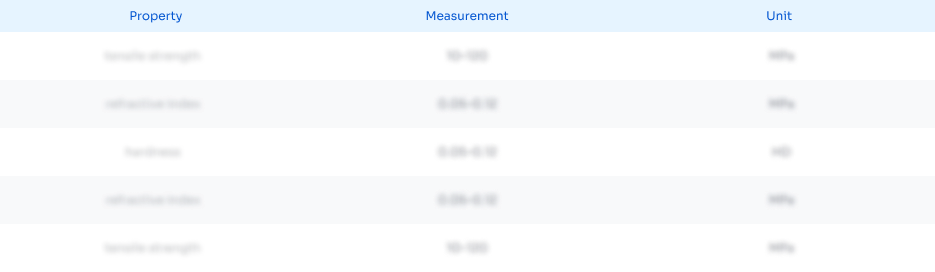
Abstract
Description
Claims
Application Information

- R&D Engineer
- R&D Manager
- IP Professional
- Industry Leading Data Capabilities
- Powerful AI technology
- Patent DNA Extraction
Browse by: Latest US Patents, China's latest patents, Technical Efficacy Thesaurus, Application Domain, Technology Topic, Popular Technical Reports.
© 2024 PatSnap. All rights reserved.Legal|Privacy policy|Modern Slavery Act Transparency Statement|Sitemap|About US| Contact US: help@patsnap.com