Underfloor heating cushion gypsum based self-leveling mortar with heat insulation performance and preparation method
A technology of thermal insulation performance and self-leveling mortar, which is applied in the field of building floor materials, can solve the problems of low market acceptance and impact on concrete bases, and achieve sustainable development, moderate foaming effect, and uniform pores Effect
- Summary
- Abstract
- Description
- Claims
- Application Information
AI Technical Summary
Problems solved by technology
Method used
Image
Examples
preparation example Construction
[0028] A method for preparing a floor heating cushion gypsum-based self-leveling mortar with thermal insulation performance, the steps are as follows:
[0029] S1. Preparation of α-type high-strength gypsum powder: CaCl 2 Put the solution into chlor-alkali industrial wastewater for full reaction, filter the reacted solution to obtain solid CaSO 4 2H 2 O, CaSO 4 2H 2 O configured as a suspension will contain CaSO 4 2H 2 The O suspension is added with a crystal-transforming agent for hydrothermal reaction, and finally α-type high-strength gypsum powder is obtained by centrifugation, drying, and grinding.
[0030] S2. Preparation of self-leveling mortar: fully mix α high-strength gypsum powder, cement, fly ash, filler, aggregate, foaming agent, foam stabilizer, water retaining agent, water reducing agent, and setting retarder to form a powder, and then Add water to the powder and stir thoroughly, control the water-material ratio to 0.21-0.25, and finally obtain gypsum-based...
Embodiment 1
[0033] In terms of mass, the mix ratio is as follows: 43 parts of α high-strength gypsum powder prepared by chlor-alkali industry by-product chemical gypsum, 8 parts of ordinary silicon cement with P.O42.5, 3 parts of secondary fly ash, 8 parts of heavy calcium powder, quartz 40 parts of sand, 0.2 parts of tea saponin, 0.1 part of triethanolamine, 0.2 parts of low viscosity hydroxypropyl methylcellulose ether, 0.2 parts of carboxylic acid water reducer and polyester water reducer, 0.05 part of trisodium citrate, The ratio of water to material is 0.233.
Embodiment 2
[0035] In terms of mass, the mix ratio is as follows: 46 parts of α high-strength gypsum powder prepared by chemical gypsum, a by-product of the chlor-alkali industry, 6 parts of ordinary silicon cement with P.O42.5, 8 parts of heavy calcium powder, 40 parts of yellow sand, and 0.6 parts of tea saponin 0.15 parts, 0.15 parts of alkanolamide, 0.15 parts of low-viscosity hydroxypropyl methylcellulose ether, 0.2 parts of BASF F10 and polyether superplasticizer, 0.05 parts of SG-10, and the ratio of water to material is 0.235.
PUM
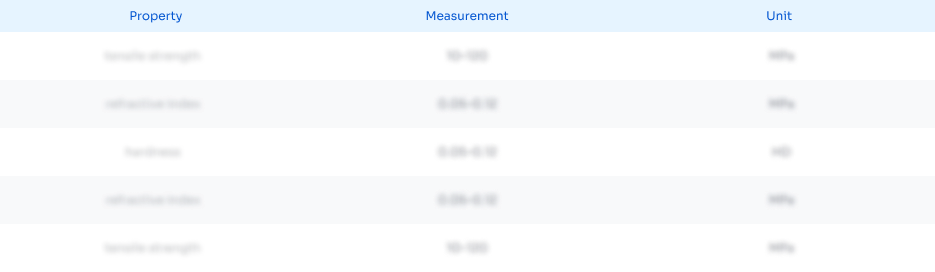
Abstract
Description
Claims
Application Information

- Generate Ideas
- Intellectual Property
- Life Sciences
- Materials
- Tech Scout
- Unparalleled Data Quality
- Higher Quality Content
- 60% Fewer Hallucinations
Browse by: Latest US Patents, China's latest patents, Technical Efficacy Thesaurus, Application Domain, Technology Topic, Popular Technical Reports.
© 2025 PatSnap. All rights reserved.Legal|Privacy policy|Modern Slavery Act Transparency Statement|Sitemap|About US| Contact US: help@patsnap.com