Zirconium oxide inkjet printing ink as well as preparation method and application thereof
A technology of inkjet printing and zirconia, applied in applications, inks, household utensils, etc., can solve problems such as film differences, and achieve the effect of low volatilization speed and good compatibility
- Summary
- Abstract
- Description
- Claims
- Application Information
AI Technical Summary
Problems solved by technology
Method used
Image
Examples
Embodiment
[0025] (1) Zirconium oxychloride octahydrate and polyethylene glycol 20000 are added to a mixed solvent of ethylene glycol and deionized water at a volume ratio of 1:1, the concentration of zirconium oxychloride octahydrate is 0.5M, polyethylene glycol The mass fraction of diol 20000 is 5%, and the zirconia inkjet printing ink is obtained by magnetically stirring and dissolving evenly and then aging for 24 hours. The obtained ink has a viscosity of 13-16 cps and a surface tension of 35-40 dyn / cm.
[0026] (2) Fill the ink obtained above into the cartridge of an inkjet printer. The printer used is Dimatix2800, and the substrate used is glass. When printing, the glass substrate should be kept at 50-60°C, the ink drop speed is 10m / s, and the nozzle does not heat up. The distance between ink droplets can be 20-45 μm. Then the printed film is heat-treated, and the heat treatment adopts the gradient heating mode. The heat treatment temperature of the printed film is first raised to...
PUM
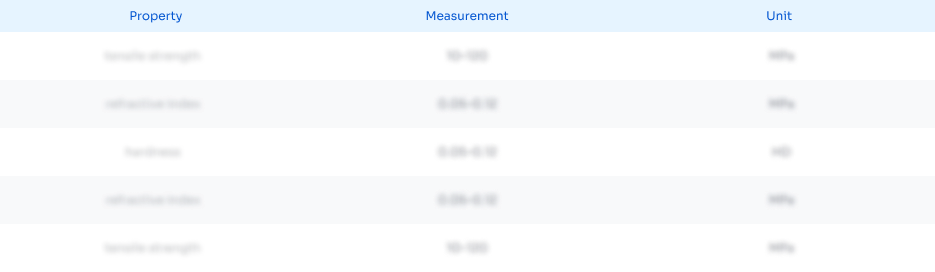
Abstract
Description
Claims
Application Information

- R&D
- Intellectual Property
- Life Sciences
- Materials
- Tech Scout
- Unparalleled Data Quality
- Higher Quality Content
- 60% Fewer Hallucinations
Browse by: Latest US Patents, China's latest patents, Technical Efficacy Thesaurus, Application Domain, Technology Topic, Popular Technical Reports.
© 2025 PatSnap. All rights reserved.Legal|Privacy policy|Modern Slavery Act Transparency Statement|Sitemap|About US| Contact US: help@patsnap.com