Microcrystalline graphite high temperature pretreatment-alkaline acid method purification method
A technology of microcrystalline graphite and purification method, applied in chemical instruments and methods, inorganic chemistry, non-metallic elements, etc., can solve the problem of low effect, and achieve the effect of improving recovery rate, improving alkali leaching efficiency, and reducing alkali leaching temperature
- Summary
- Abstract
- Description
- Claims
- Application Information
AI Technical Summary
Problems solved by technology
Method used
Examples
Embodiment 1
[0027] S1. The microcrystalline graphite ore with a carbon content of 70% is crushed and ground to a particle size of 100 mesh;
[0028] S2. heat-treating the finely ground microcrystalline graphite powder obtained in step S1 at 500° C. for 3 minutes;
[0029] S3. Mix the mineral after the heat treatment in step S2 with 20% sodium hydroxide solution while it is hot, and carry out pressurized alkaline leaching under the conditions of a liquid-solid ratio of ore slurry of 10:1, a temperature of 100°C, a reaction time of 2 hours, and a pressure of 0.6 MPa. The leached slag was washed with water and dried at 80°C for 3 hours to obtain alkali leached graphite;
[0030] S4. After mixing the alkali leached graphite and 10% HCl solution obtained in step S3, carry out acid leaching at normal pressure under the conditions of slurry liquid-solid ratio 10:1, temperature 110°C, and reaction time 3h, and the leached slag is washed with water and heated at 80°C. After drying for 3 hours, a ...
Embodiment 2
[0032] S1. The microcrystalline graphite ore with a carbon content of 82.8% is crushed and ground to a particle size of 140 mesh;
[0033] S2. heat-treating the finely ground microcrystalline graphite powder obtained in step S1 at 600° C. for 3 minutes;
[0034] S3. Mix the mineral after the heat treatment in step S2 with 10% sodium hydroxide solution while it is hot, and carry out pressurized alkaline leaching under the conditions of a liquid-solid ratio of ore slurry of 12:1, a temperature of 110°C, a reaction time of 2 hours, and a pressure of 0.6 MPa. The leached slag was washed with water and dried at 80°C for 3 hours to obtain alkali leached graphite;
[0035] S4. After mixing the alkali leached graphite and 10% HCl solution obtained in step S3, carry out acid leaching at normal pressure under the conditions of slurry liquid-solid ratio 10:1, temperature 114°C, and reaction time 2h. After drying for 3 hours, a microcrystalline graphite product with a fixed carbon conten...
Embodiment 3
[0037] S1. The microcrystalline graphite ore with a carbon content of 84.6% is crushed and ground to a particle size of 200 mesh;
[0038] S2. heat-treating the finely ground microcrystalline graphite powder obtained in step S1 at 800° C. for 3 minutes;
[0039] S3. Mix the mineral after the heat treatment in step S2 with 10% sodium hydroxide solution while it is hot, and carry out pressurized alkaline leaching under the conditions of ore slurry liquid-solid ratio 11:1, temperature 115°C, reaction time 2.5h, and pressure 0.8 MPa , the leached slag was washed with water and dried at 80°C for 3 hours to obtain alkali leached graphite;
[0040] S4. After mixing the alkali leached graphite and 10% HCl solution obtained in step S3, carry out acid leaching at normal pressure under the conditions of slurry liquid-solid ratio 11:1, temperature 115°C, and reaction time 2.5h. The leached residue is washed with water and heated at 100°C. After drying at high temperature for 3 hours, a m...
PUM
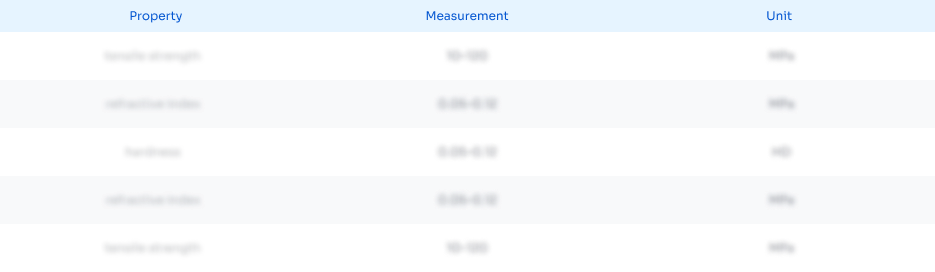
Abstract
Description
Claims
Application Information

- R&D
- Intellectual Property
- Life Sciences
- Materials
- Tech Scout
- Unparalleled Data Quality
- Higher Quality Content
- 60% Fewer Hallucinations
Browse by: Latest US Patents, China's latest patents, Technical Efficacy Thesaurus, Application Domain, Technology Topic, Popular Technical Reports.
© 2025 PatSnap. All rights reserved.Legal|Privacy policy|Modern Slavery Act Transparency Statement|Sitemap|About US| Contact US: help@patsnap.com