Method for preparing denitration catalyst by recycling raw material from waste catalyst
A technology of waste catalyst and denitration catalyst, applied in the field of denitration catalyst, can solve the problems of short life, low catalytic efficiency, poor denitration catalyst activity, etc., and achieve the effect of reducing investment
- Summary
- Abstract
- Description
- Claims
- Application Information
AI Technical Summary
Problems solved by technology
Method used
Image
Examples
Embodiment 1
[0070] The recovery method of spent denitrification catalyst comprises the following sequential steps:
[0071] Wash and dry the scrapped denitrification catalyst with a mass percent concentration of 20% nitric acid solution for 16 hours to remove impurities on the surface of the catalyst; use a mass percent concentration of 30% sodium hydroxide solution to clean the spent catalyst after the above pickling Soak to remove arsenic and its compounds. The cleaning time is 16 hours. The spent catalyst after arsenic removal is cleaned with sodium hydrogen sulfide solution to remove mercury. The mass percentage concentration of sodium hydrogen sulfide solution is 15%, and the cleaning time is 15 hours. Water cleaning, drying, calcination, crushing, jet crushing and other processes, deionized water cleaning time is 12h, drying temperature is 120°C, drying time is 12h, calcination temperature is 550°C, calcination time is 12h, the median particle size after crushing The denitration pow...
Embodiment 2
[0089] The recovery method of spent denitrification catalyst comprises the following sequential steps:
[0090] Wash and dry the scrapped denitrification catalyst with a mass percentage concentration of 26% nitric acid solution for 20 hours to remove impurities on the surface of the catalyst; use a mass percentage concentration of 35% sodium hydroxide solution to clean the waste catalyst after the above pickling Soak to remove arsenic and its compounds. The cleaning time is 20 hours. The waste catalyst after arsenic removal is cleaned and mercury is removed with sodium hydrogen sulfide solution. The mass percentage concentration of sodium hydrogen sulfide solution is 20%, and the cleaning time is 16 hours. Water cleaning, drying, calcination, crushing, jet crushing and other processes, deionized water cleaning time is 16h, drying temperature is 130°C, drying time is 14h, calcination temperature is 600°C, calcination time is 16h, the median particle size after crushing The deni...
Embodiment 3
[0108] The recovery method of spent denitrification catalyst comprises the following sequential steps:
[0109] Wash and dry the spent denitrification catalyst with a mass percent concentration of 15% nitric acid solution for 10 hours to remove impurities on the surface of the catalyst; use a mass percent concentration of 15% sodium hydroxide solution to clean the waste catalyst after the above pickling Soak to remove arsenic and its compounds. The cleaning time is 10 hours. The waste catalyst after arsenic removal is cleaned with sodium hydrogen sulfide solution to remove mercury. The mass percentage concentration of sodium hydrogen sulfide solution is 10%, and the cleaning time is 11 hours. Water cleaning, drying, calcination, crushing, jet crushing and other processes, deionized water cleaning time is 11h, drying temperature is 80°C, drying time is 10h, calcination temperature is 450°C, calcination time is 10h, the median particle size after crushing The denitration powder ...
PUM
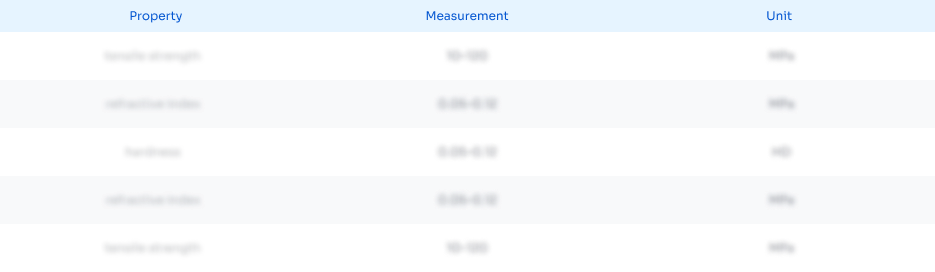
Abstract
Description
Claims
Application Information

- R&D
- Intellectual Property
- Life Sciences
- Materials
- Tech Scout
- Unparalleled Data Quality
- Higher Quality Content
- 60% Fewer Hallucinations
Browse by: Latest US Patents, China's latest patents, Technical Efficacy Thesaurus, Application Domain, Technology Topic, Popular Technical Reports.
© 2025 PatSnap. All rights reserved.Legal|Privacy policy|Modern Slavery Act Transparency Statement|Sitemap|About US| Contact US: help@patsnap.com