Preparation method of steel strip covered by ferronickel/nickel-cobalt double coatings
A technology of steel strip and nickel-cobalt, which is applied in the field of steel strip preparation, can solve problems affecting battery storage life and battery leakage, and achieve the effects of improving cracks in the coating, prolonging service life, and enhancing corrosion resistance
- Summary
- Abstract
- Description
- Claims
- Application Information
AI Technical Summary
Problems solved by technology
Method used
Image
Examples
preparation example Construction
[0018] The invention provides a method for preparing a steel strip covered by a nickel-iron / nickel-cobalt double coating, comprising the following steps:
[0019] Step 1: First mix sodium carbonate, sodium phosphate dodecahydrate, sodium silicate and sodium hydroxide with a mass ratio of 0.5-12:3-24:0.2-4:1-3 to form the first mixture, and then mix the steel The strip is placed in the first mixture, and placed at the first preset temperature for the first preset time; then the steel strip is soaked in 20vol%-45vol% sulfuric acid for the second preset time, and then at 5vol%-15vol After soaking in % sulfuric acid for a third preset time, activate it to remove the residual impurities on the surface of the steel strip to obtain the steel strip body;
[0020] Step 2: first mix nickel sulfate hexahydrate, nickel chloride hexahydrate, boric acid, and sodium lauryl sulfate with a mass ratio of 5-8:1-2:0.5-1.5:0.001-0.05 to form a second mixture, Then place the steel strip body obtai...
Embodiment
[0029] Step 1: first mix sodium carbonate, sodium phosphate dodecahydrate, sodium silicate and sodium hydroxide at a mass ratio of 0.5:3:0.2:1 to form the first mixture, then place the steel strip in the first mixture, and place it at 50°C for 20 minutes; then soak the steel strip in 20vol%-45vol% sulfuric acid for 3 minutes, then soak it in 5vol%-15vol% sulfuric acid for 8 minutes, then activate it to remove the residual impurities on the surface of the steel strip, and obtain Steel belt body.
[0030] Step 2: First mix nickel sulfate hexahydrate, nickel chloride hexahydrate, boric acid, and sodium lauryl sulfate with a mass ratio of 5:1:0.5:0.05 to form a second mixture, and then mix the steel obtained in step 1 The strip body is placed in the second mixture for the first electroplating to obtain a steel strip with a nickel-plated layer, wherein the current density of the first electroplating is 1.5A / dm 2 , PH value: 3.8, the temperature of the first electroplating: 35 ℃. ...
PUM
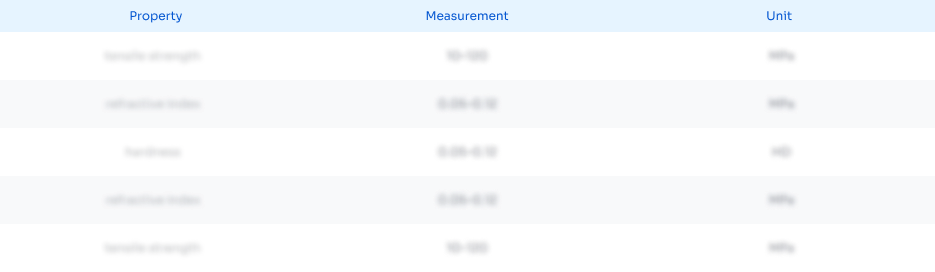
Abstract
Description
Claims
Application Information

- Generate Ideas
- Intellectual Property
- Life Sciences
- Materials
- Tech Scout
- Unparalleled Data Quality
- Higher Quality Content
- 60% Fewer Hallucinations
Browse by: Latest US Patents, China's latest patents, Technical Efficacy Thesaurus, Application Domain, Technology Topic, Popular Technical Reports.
© 2025 PatSnap. All rights reserved.Legal|Privacy policy|Modern Slavery Act Transparency Statement|Sitemap|About US| Contact US: help@patsnap.com