Dibasic acid modified epoxy stillingia oil methyl ester plasticizer and preparation method thereof
A technology of acid epoxy fatty acid ester and epoxy catalpa, which is applied in the field of oil utilization and plasticizer development, can solve the problems of low flash point, high energy consumption, poor effect, etc., and achieve the effect of increasing relative molecular weight and reducing content
- Summary
- Abstract
- Description
- Claims
- Application Information
AI Technical Summary
Problems solved by technology
Method used
Image
Examples
Embodiment 1
[0030] Raw materials: catalpa oil, methanol, hydrogen peroxide, potassium hydroxide, p-toluenesulfonic acid, maleic acid, N,N-dimethylbenzylamine;
[0031] Put methanol and catalpa oil into the reactor according to the proportion of 6:1, and add potassium hydroxide accounting for 0.6% of the mass fraction of catalpa oil, stir and reflux reaction at 65 ° C for 3 hours, remove methanol and Glycerol has obtained catalpa methyl ester; the gained catallyl methyl ester is put into the reactor, adds 15% formic acid and 1% p-toluenesulfonic acid accounting for the quality of the methyl ester, is heated to 55° C. and drips hydrogen peroxide (30 %), dripped in 40 minutes, and then heated up to 65 ° C for 4 hours. After cooling down, separate the liquid and remove the water, and then undergo conventional post-treatments such as alkali washing, water washing, distillation, etc. to obtain a light yellow transparent liquid epoxy catalphine methyl ester; put epoxy catalphine methyl ester and...
Embodiment 2
[0034] Raw materials: catalpa methyl ester, m-chloroperoxybenzoic acid, p-toluenesulfonic acid, maleic anhydride, N,N-dimethylbenzylamine;
[0035] Put catalphine methyl ester into the reactor, keep the temperature at 0-30°C, add 1.2 g of m-chloroperoxybenzoic acid solution dropwise, drop it within 1 hour, and then react for 5 hours. Finally, through certain conventional post-treatments such as filtration, alkali washing, water washing, dehydration, etc., the light yellow transparent intermediate product epoxy catalphal methyl ester is obtained; the ratio of epoxy catalphal methyl ester and maleic anhydride is 1:0.15 according to the amount of substance Put it into the reaction kettle, then add the catalyst N,N-dimethylbenzylamine accounting for 1% mass fraction of epoxy catalphine methyl ester, stir and heat up to 105°C for about 4 hours, and the acid value is 0.32mgKOH / g, Stop responding. The crude product is a reddish-brown transparent viscous liquid.
Embodiment 3
[0037] Raw materials: epoxy catalphine methyl ester, maleic anhydride, N,N-dimethylbenzylamine;
[0038] Put epoxy catalphine methyl ester and maleic anhydride in the ratio of 1:0.29 into the reaction kettle, and then add the catalyst N,N-dimethylbenzylamine which accounts for 1% mass fraction of epoxy catalphine methyl ester , stirring and raising the temperature to 120° C. for about 4 hours, the acid value was measured to be 0.51 mgKOH / g, and the reaction was stopped. The crude product is a reddish-brown transparent viscous liquid.
PUM
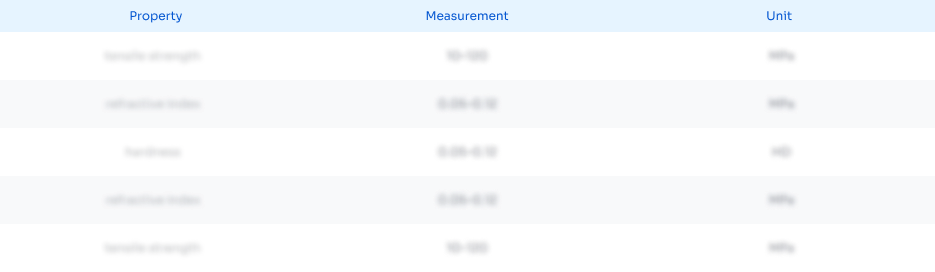
Abstract
Description
Claims
Application Information

- R&D Engineer
- R&D Manager
- IP Professional
- Industry Leading Data Capabilities
- Powerful AI technology
- Patent DNA Extraction
Browse by: Latest US Patents, China's latest patents, Technical Efficacy Thesaurus, Application Domain, Technology Topic, Popular Technical Reports.
© 2024 PatSnap. All rights reserved.Legal|Privacy policy|Modern Slavery Act Transparency Statement|Sitemap|About US| Contact US: help@patsnap.com