Method for testing electroplating current efficiency by using square Hull cell
A current efficiency, square technology, applied in the electrolysis process, electrolysis components, weighing by removing certain components, etc., can solve the problems of large deviation, large difference in cathode current density distribution, troublesome production of electricity meter, etc., to improve the accuracy The effect of high speed, simple operation and low cost
- Summary
- Abstract
- Description
- Claims
- Application Information
AI Technical Summary
Problems solved by technology
Method used
Image
Examples
Embodiment Construction
[0024] In this example, refer to figure 1 and figure 2 , the method for utilizing square Hall cell to test electroplating current efficiency is carried out in the following steps,
[0025] 1) Sampling. Before sampling, fully stir the plating solution, and sample the plating solution from different parts of the plating tank, and use it after mixing;
[0026] 2) Remove the coating on the side of the test piece that needs to be plated, use 3000# fine sandpaper or a scouring pad to polish the brass test piece in one direction, and dry it at 50ºC for later use;
[0027] 3) Take 500ml of the plating solution sampled in step 1) and put it into the square Hall tank, heat the plating solution to the process temperature, and turn on the air stirring during the heating process to avoid local overheating and decompose the additive; the plating solution cannot be heated If the temperature is too high, it cannot fully reflect the original state of the plating solution even after cooling;...
PUM
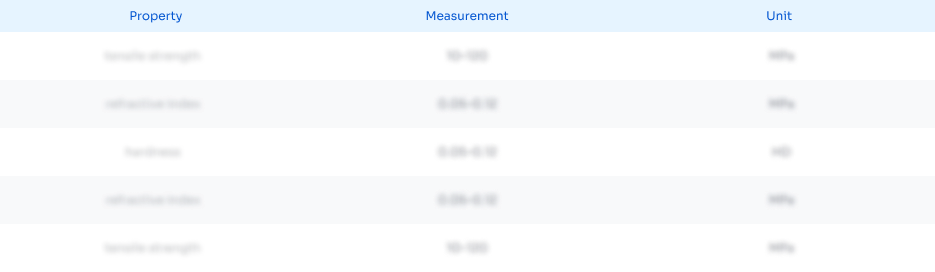
Abstract
Description
Claims
Application Information

- R&D
- Intellectual Property
- Life Sciences
- Materials
- Tech Scout
- Unparalleled Data Quality
- Higher Quality Content
- 60% Fewer Hallucinations
Browse by: Latest US Patents, China's latest patents, Technical Efficacy Thesaurus, Application Domain, Technology Topic, Popular Technical Reports.
© 2025 PatSnap. All rights reserved.Legal|Privacy policy|Modern Slavery Act Transparency Statement|Sitemap|About US| Contact US: help@patsnap.com