W-shaped flame boiler grading combustion method
A staged combustion, staged combustion technology, applied in the direction of combustion method, staged combustion, combustion chamber, etc., can solve the problem of slagging in the cold ash hopper under the flame, complicated boiler structure, and the flame floating directly into the burnout chamber in the aerodynamic field, etc. question
- Summary
- Abstract
- Description
- Claims
- Application Information
AI Technical Summary
Problems solved by technology
Method used
Image
Examples
Embodiment 1
[0088] Such as figure 2 As shown, the staged combustion method of the W-shaped flame boiler in this embodiment, four ventilation slits are opened longitudinally in the wing wall to blow the secondary air inward, the outer diameter of the water-cooled wall tube at the wing wall is relatively large (120.65mm), and the center distance is 146.4mm. The pipe gap is 25.4mm, and the outer diameter of the upper and lower pipes on the wing wall is small (69.85mm). The original design connects the two ends through the reducing pipe, and only needs to replace the thick pipes at the four ventilation belts that need to be ventilated with thin ones. tube (move the position of the upper and lower heads down), the gap between the tubes can be widened to 76.55mm, the ventilation effect is good, and it can prevent large-area coking of the wing wall water-cooled wall tubes. figure 2 shown. The height of the ventilation belt can be set to the total length of the wing wall pipes, or only set on ...
Embodiment 2
[0113] The staged combustion method of the W-type flame boiler in this embodiment includes:
[0114] Select several coal types, and conduct coal quality element and industrial analysis on the selected coal types based on thermogravimetric and infrared analysis;
[0115] Based on the coal quality elements and industrial analysis results, the combustion strategy of the boiler is predetermined, and the combustion strategy specifically includes: (1) the proportion of coal types that can form staged combustion in the boiler and the corresponding coal pulverizer coal grinding method ; (2) Can not form the proportion of classified coal configuration in the boiler and the corresponding coal mill coal grinding method; wherein, the classified combustion of the boiler is specifically: using combustible coal to react with oxygen to become the first-stage combustion , where the combustible coal is bituminous coal or a mixture of bituminous coal and lean coal; the high-temperature flue gas ...
Embodiment 3
[0175] The staged combustion method of the W-type flame boiler in this embodiment, on the basis of Embodiment 1, also includes: the steps of determining the F wind downtilt angle F wind downtilt angle and the D and E wind openings, specifically including:
[0176] Under the conditions of the following three loads (1), (2) and (3) and F wind downtilt angle, the boiler adopts the fuel staged combustion method to burn, and obtains the operation status of the secondary air downtilt angle in different F layers , wherein the operating conditions at least include: NOx, CO, O2 of the flue gas at the outlet of the economizer; NOx, CO, O2 of the flue gas at the outlet of the air preheater; the thermal efficiency of the boiler; Slag sampling analysis; economizer outlet flue gas temperature; air preheater outlet flue gas temperature; raw coal sampling; ambient temperature, humidity and atmospheric pressure;
[0177] Among them, (1) under the 325MW load, the F wind downtilt angle is 0゜, 10...
PUM
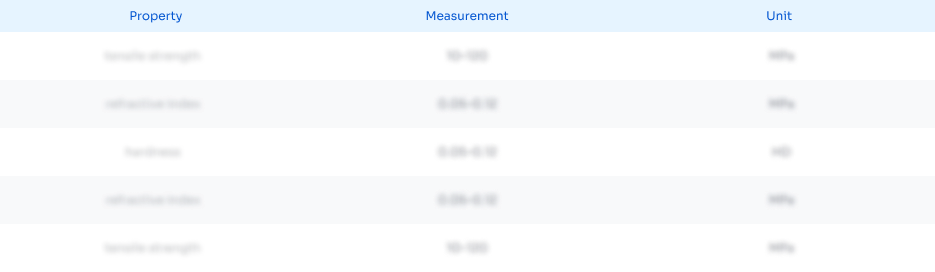
Abstract
Description
Claims
Application Information

- R&D
- Intellectual Property
- Life Sciences
- Materials
- Tech Scout
- Unparalleled Data Quality
- Higher Quality Content
- 60% Fewer Hallucinations
Browse by: Latest US Patents, China's latest patents, Technical Efficacy Thesaurus, Application Domain, Technology Topic, Popular Technical Reports.
© 2025 PatSnap. All rights reserved.Legal|Privacy policy|Modern Slavery Act Transparency Statement|Sitemap|About US| Contact US: help@patsnap.com