Radiation-proof anti-cracking heat-insulating concrete
A thermal insulation concrete and radiation protection technology, applied in the field of thermal insulation concrete, can solve problems such as cracking damage, volume deformation, etc., achieve the effects of improving strength, overcoming poor toughness, and remarkable early strength effect
- Summary
- Abstract
- Description
- Claims
- Application Information
AI Technical Summary
Problems solved by technology
Method used
Examples
Embodiment 1
[0015] Concrete components include 70 parts by weight of cement, 10 parts of zirconia, 4 parts of silicon micropowder, 5 parts of sodium silicate, 10 parts of sodium fluorosilicate, 10 parts of barite, 5 parts of carbon fiber, and hard boron calcium 4 parts of stone, 3 parts of polyurethane particles, 8 parts of cyanite honeycomb ceramic powder, 5 parts of polyethylene glycol monomethyl ether methacrylate, and 3 parts of calcium lignosulfonate.
[0016] The preparation method of the present embodiment comprises the following steps:
[0017] A. After mixing zirconia, silicon micropowder, sodium silicate, sodium fluorosilicate, barite, colemanite, polyurethane particles, and bluestone honeycomb ceramic powder, add them to the pulverizer and grind them at a speed of 1200 rpm. The crushing time was 20min to obtain mixture A;
[0018] B. Add carbon fiber, polyethylene glycol monomethyl ether methacrylate, and calcium lignosulfonate to mixture A, mix and add to a heating tank for h...
Embodiment 2
[0021] Concrete components include 100 parts by weight of cement, 20 parts of zirconia, 12 parts of silicon micropowder, 10 parts of sodium silicate, 20 parts of sodium fluorosilicate, 20 parts of barite, 12 parts of carbon fiber, and hard boron calcium 12 parts of stone, 9 parts of polyurethane particles, 18 parts of bluestone honeycomb ceramic powder, 12 parts of polyethylene glycol monomethyl ether methacrylate, and 9 parts of calcium lignosulfonate.
[0022] The preparation method of the present embodiment comprises the following steps:
[0023] A. After mixing zirconia, silicon micropowder, sodium silicate, sodium fluorosilicate, barite, colemanite, polyurethane particles, and bluestone honeycomb ceramic powder, add them to the pulverizer and grind them at a speed of 1200 rpm. The crushing time was 20min to obtain mixture A;
[0024] B. Add carbon fiber, polyethylene glycol monomethyl ether methacrylate, and calcium lignosulfonate to mixture A, mix and add to a heating t...
Embodiment 3
[0027] Concrete components include 75 parts by weight of cement, 12 parts of zirconia, 6 parts of silicon micropowder, 6 parts of sodium silicate, 12 parts of sodium fluorosilicate, 12 parts of barite, 6 parts of carbon fiber, and hard boron calcium 5 parts of stone, 4 parts of polyurethane particles, 9 parts of cyanite honeycomb ceramic powder, 7 parts of polyethylene glycol monomethyl ether methacrylate, and 4 parts of calcium lignosulfonate.
[0028] The preparation method of the present embodiment comprises the following steps:
[0029] A. After mixing zirconia, silicon micropowder, sodium silicate, sodium fluorosilicate, barite, colemanite, polyurethane particles, and bluestone honeycomb ceramic powder, add them to the pulverizer and grind them at a speed of 1200 rpm. The crushing time was 20min to obtain mixture A;
[0030] B. Add carbon fiber, polyethylene glycol monomethyl ether methacrylate, and calcium lignosulfonate to mixture A, mix and add to a heating tank for h...
PUM
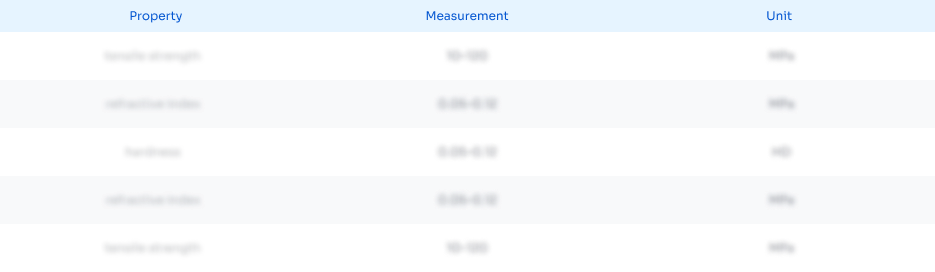
Abstract
Description
Claims
Application Information

- R&D
- Intellectual Property
- Life Sciences
- Materials
- Tech Scout
- Unparalleled Data Quality
- Higher Quality Content
- 60% Fewer Hallucinations
Browse by: Latest US Patents, China's latest patents, Technical Efficacy Thesaurus, Application Domain, Technology Topic, Popular Technical Reports.
© 2025 PatSnap. All rights reserved.Legal|Privacy policy|Modern Slavery Act Transparency Statement|Sitemap|About US| Contact US: help@patsnap.com