Method for eliminating leaching toxicity of heavy metal solid waste residues
A technology for heavy metals and waste residues, which is used in the improvement of process efficiency and other directions
- Summary
- Abstract
- Description
- Claims
- Application Information
AI Technical Summary
Problems solved by technology
Method used
Examples
Embodiment 1
[0017] For cobalt hydrometallurgical solid waste containing 0.25% cobalt, 0.12% vanadium, 0.02% nickel, 0.01% copper, 0.03% manganese, etc., remove iron by dry magnetic separation, and add 1‰ calcium chloride and 2‰ sodium pyrosulfite Mix evenly, add to the bottom of the stainless steel acid-resistant tank to pave; add 0.03M dilute sulfuric acid solution at a liquid-solid ratio of 10:1 (L / kg), and soak for 2 hours at room temperature; add flocculant polyacrylamide to the tank, A titanium mesh is placed in the liquid as the positive electrode, and the tank body is the other electrode. During the leaching process, the current density is 30A / m 2 , the tank voltage is 1.2V, the two poles are interchanged during the electric assisted leaching process, the cycle is 50 minutes of forward energization, and then reverse energization for 1 minute, and the total electric assisted leaching time is 3 hours; after leaching, remove the titanium mesh electrode, stir and filter; the filtrate V...
Embodiment 2
[0019] For zinc hydrometallurgical solid waste slag containing 0.33% zinc, 0.05% cobalt, 0.19% vanadium, 0.08% copper, 0.17% manganese, etc., remove iron through dry magnetic separation, add 2‰ calcium carbonate and 5‰ sodium sulfite to mix evenly Add 0.4M dilute sulfuric acid at room temperature for 3 hours at room temperature according to the liquid-solid ratio of 7:1 (L / kg); add flocculant polyacrylamide into the tank, and place lead in the leaching solution The base alloy is used as the positive electrode, and the tank body is the other electrode. During the leaching process, the current density is 60A / m 2 , the tank voltage is 3.1V, the two poles are interchanged during the electric assisted leaching process, the cycle is forward energization for 30min, and then reverse energization for 1min, the total electric assisted leaching time is 2h; after leaching, remove the alloy electrode, stir and filter; filtrate recovery Zinc, vanadium, copper, cobalt, manganese and other va...
Embodiment 3
[0021] For chromium hydrometallurgical solid waste containing 0.06% chromium, 0.09% vanadium, 0.015% lead, 0.04% copper, and 0.02% manganese, remove iron by dry magnetic separation, and add 3‰ calcium chloride and 3‰ thiosulfuric acid Mix the sodium evenly, add the bottom of the titanium acid-resistant tank and pave it; add 0.05M dilute sulfuric acid at room temperature for 1 hour at a liquid-solid ratio of 10:1 (L / kg); add flocculant polyacrylamide to the tank, Place a ruthenium-based multi-component mixture coating in the solution to modify the titanium plate and titanium mesh as the positive electrode, and the tank body is the other electrode. During the leaching process, the current density is 70A / m 2 , the tank voltage is 3.2V, and the two poles are interchanged during the electric-assisted leaching process. The cycle is forward energization for 40 minutes, and then reverse energization for 1 minute, and the total electric-assisted leaching time is 1.5h; Valuable metal el...
PUM
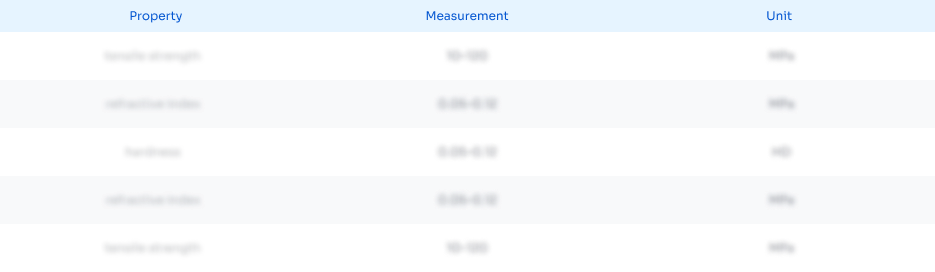
Abstract
Description
Claims
Application Information

- Generate Ideas
- Intellectual Property
- Life Sciences
- Materials
- Tech Scout
- Unparalleled Data Quality
- Higher Quality Content
- 60% Fewer Hallucinations
Browse by: Latest US Patents, China's latest patents, Technical Efficacy Thesaurus, Application Domain, Technology Topic, Popular Technical Reports.
© 2025 PatSnap. All rights reserved.Legal|Privacy policy|Modern Slavery Act Transparency Statement|Sitemap|About US| Contact US: help@patsnap.com