Magnetic plastic and preparation method thereof
A magnetic and plastic technology, applied in the field of plastics, can solve the problems of unstable performance of magnetic plastics, poor combination of magnetic powder and plastic body, non-uniform magnetic plastics, etc., and achieve the goal of improving combination compatibility, ensuring uniformity and stability Effect
- Summary
- Abstract
- Description
- Claims
- Application Information
AI Technical Summary
Problems solved by technology
Method used
Examples
preparation example Construction
[0025] The invention also discloses a preparation method of magnetic plastics, comprising the following steps:
[0026] S1: preparation of hyperbranched polysiloxane-grafted silica-coated ferric oxide particles;
[0027] S2: After mixing polyphenylene ether, silicone resin, lubricant, plasticizer and stabilizer evenly, heat, melt and stir in a high-speed mixer to obtain a polymerization mixture;
[0028] S3: Add the ferric oxide particles coated with hyperbranched polysiloxane grafted with silicon dioxide prepared in step S1 to the polymerization mixture prepared in step S2, and stir to make the ferric oxide particles coated on the surface of the ferric oxide particles The hyperbranched polysiloxane is evenly dispersed in the polymerization mixture; then it is placed in a mold, and after vacuum defoaming, it is solidified by a stepwise heating method, and then cooled to room temperature to obtain a magnetic plastic.
[0029] Wherein, in step S1, the following steps are includ...
Embodiment 1
[0037] This embodiment discloses a magnetic plastic, which includes the following components in parts by weight: 60 parts of polyphenylene ether, 15 parts of polyalkyl silicone resin, 3 parts of pentaerythritol stearate, phthalates 8 parts of plasticizer, 1 part of calcium stearate and 5 parts of magnetic particles, the magnetic particles are ferric oxide particles coated with silicon dioxide grafted by hyperbranched polysiloxane.
[0038] The preparation method of the magnetic plastic comprises the following steps:
[0039] S1: Preparation of ferric oxide particles coated with silicon dioxide grafted with hyperbranched polysiloxane, specifically:
[0040] S11: Take magnetic Fe3O4 nanoparticles, ultrasonically disperse them in n-propanol solvent, add ammonia water dropwise under stirring conditions to make the pH 8.0-11.0, then add ethyl orthosilicate, and react at 25-60°C 2-6h, magnetic separation to obtain ferric oxide particles coated with silicon dioxide; wherein, the mas...
Embodiment 2
[0046] This embodiment discloses a magnetic plastic, which includes the following components in parts by weight: 80 parts of polyphenylene ether, 5 parts of polyalkyl silicone resin, 5 parts of pentaerythritol stearate, phthalates 10 parts of plasticizer, 2 parts of calcium stearate and 4 parts of magnetic particles, the magnetic particles are ferric oxide particles coated with silicon dioxide grafted by hyperbranched polysiloxane.
[0047] The preparation method of the magnetic plastic comprises the following steps:
[0048] S1: Preparation of ferric oxide particles coated with silicon dioxide grafted with hyperbranched polysiloxane, specifically:
[0049] S11: Take magnetic Fe3O4 nanoparticles, ultrasonically disperse them in n-propanol solvent, add ammonia water dropwise under stirring conditions to make the pH 8.0-11.0, then add ethyl orthosilicate, and react at 25-60°C 2-6h, magnetic separation to obtain ferric oxide particles coated with silicon dioxide; wherein, the ma...
PUM
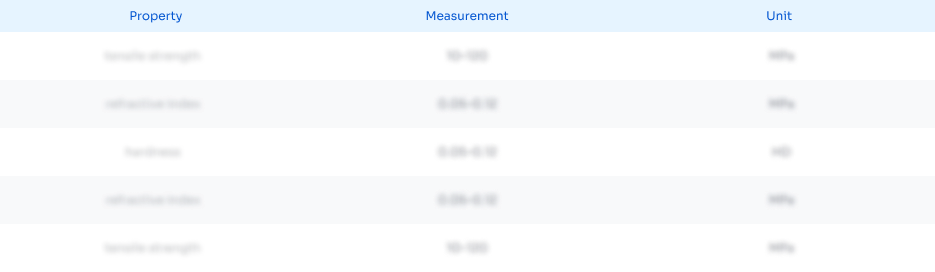
Abstract
Description
Claims
Application Information

- R&D
- Intellectual Property
- Life Sciences
- Materials
- Tech Scout
- Unparalleled Data Quality
- Higher Quality Content
- 60% Fewer Hallucinations
Browse by: Latest US Patents, China's latest patents, Technical Efficacy Thesaurus, Application Domain, Technology Topic, Popular Technical Reports.
© 2025 PatSnap. All rights reserved.Legal|Privacy policy|Modern Slavery Act Transparency Statement|Sitemap|About US| Contact US: help@patsnap.com