Steel for front axle of medium-sized truck and production method of steel
A technology for medium-sized trucks and front axles, which is applied in the steel for medium-sized trucks' front axles and its production field. It can solve the problems that the steel quality is difficult to meet the fatigue life of the front axle of automobiles, achieve uniform and stable composition and structure, improve pouring performance, and steel properties. excellent effect
- Summary
- Abstract
- Description
- Claims
- Application Information
AI Technical Summary
Problems solved by technology
Method used
Image
Examples
Embodiment 1
[0021] A 120-ton electric furnace is used for primary smelting, using high-quality self-circulating scrap steel, adding 84.9 tons of molten iron, accounting for 69.19%, adding 26kg of copper with the scrap steel, smelting in the electric furnace for 55 minutes, power supply for 10 minutes, the end carbon 0.12%, the end phosphorus 0.009%, and tapping The temperature is 1638°C. 115 tons of steel are tapped from the electric furnace, 500kg of lime is added during the tapping process, 400kg of refined pre-slag is added, and alloys are added into the production line according to the composition. After the molten steel reaches the refining station, a total of 470kg of lime and 290kg of pre-smelting slag are added during the power transmission process, and calcium carbide, carburizer and silicon carbide are used for diffusion deoxidation, and 50kg of silicon carbide is used. After the diffusion deoxidation is completed, the alloy is allocated according to the target composition. The ...
Embodiment 2
[0042] Use a 120-ton electric furnace for smelting, add 40.7 tons of scrap steel, add 25kg of copper with the scrap steel, add 79.7 tons of molten iron, the ratio of molten iron is 66.42%, smelt in the electric furnace for 65 minutes, send electricity for 13 minutes, end-point carbon 0.12%, end-point phosphorus 0.009%, tapping temperature 1641 ℃, the steel output of the electric furnace is 117.5 tons. During the tapping process, 900kg of lime is added along with the steel flow, 250kg of refined pre-slag is added, and the alloy is mixed according to the lower limit of the composition. After the molten steel reaches the refining station, power is sent. According to the fluidity of the slag, 200kg of lime is supplemented, 450kg of refined pre-slag is used, and carburizers and silicon carbide are used for diffusion deoxidation, and silicon carbide is used for 55kg. into the alloy, the total refining cycle is 55min. After the molten steel is refined, carry out vacuum degassing, va...
PUM
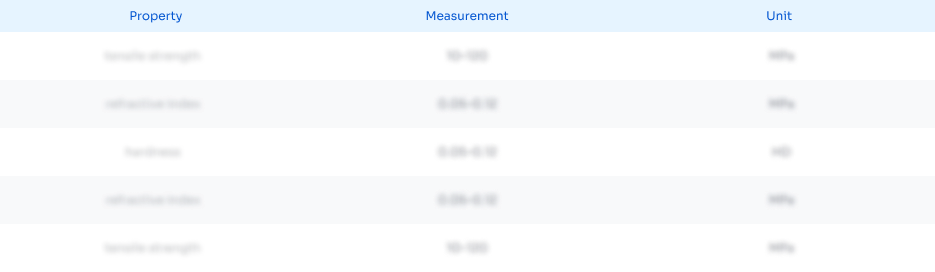
Abstract
Description
Claims
Application Information

- R&D
- Intellectual Property
- Life Sciences
- Materials
- Tech Scout
- Unparalleled Data Quality
- Higher Quality Content
- 60% Fewer Hallucinations
Browse by: Latest US Patents, China's latest patents, Technical Efficacy Thesaurus, Application Domain, Technology Topic, Popular Technical Reports.
© 2025 PatSnap. All rights reserved.Legal|Privacy policy|Modern Slavery Act Transparency Statement|Sitemap|About US| Contact US: help@patsnap.com