Method for respectively recycling copper, nickel and zinc from electroplating sludge
A technology of electroplating sludge and sponge copper, which is applied in the field of iron, high copper, nickel, zinc treatment process, separation and value of calcium, zinc, copper in high zinc electroplating sludge, and copper in electroplating sludge respectively, It can solve the problems of secondary waste, resource waste, and large amount of alkali consumption, and achieve the effects of reducing environmental hazards, strong applicability, and simple operation
- Summary
- Abstract
- Description
- Claims
- Application Information
AI Technical Summary
Problems solved by technology
Method used
Image
Examples
Embodiment 1
[0037] Get 600kg of electroplating sludge (hereinafter referred to as solid waste, its main components are Cu, Ni, Zn, Ca, Fe) produced by a certain factory, put the electroplating sludge into 1# reactor, add 0.9t of 10wt% dilute sulfuric acid , normal temperature, after fully stirring for 0.5h, the leaching ends, and the solution is poured into a filter press, filtered and separated to obtain calcium sulfate product and solution ①, which contains Zn 2+ 、Cu 2+ 、Ni 2+ , Fe 2+ , Fe 3+ ;
[0038] Pour the solution ① into the 2# reaction kettle, add 1 times the theoretical amount of iron powder, stir at room temperature for 1 hour, pour it into the filter, filter to obtain sponge copper and solution ②, the solution ② contains Zn 2+ 、Ni 2+ , Fe 2+ , Fe 3+ ;
[0039] Put the solution ② into the dissolution tank, use the aeration device to aerate with oxygen for 4 hours, and the aeration volume is 2m 3 / h, the oxygen concentration is 20%, and utilize steam to heat solution ②...
Embodiment 2
[0044]Take 800kg of electroplating sludge (hereinafter referred to as solid waste, its main components are Cu, Ni, Zn, Ca, Fe) produced by a certain factory, put the electroplating sludge into 1# reactor, add 1.6t of 10wt% concentrated sulfuric acid , normal temperature, after fully stirring for 1.5h, the leaching ends, and the solution is poured into a filter press, filtered and separated to obtain calcium sulfate product and solution ①, which contains Zn 2+ 、Cu 2+ 、Ni 2+ , Fe 2+ , Fe 3+ ;
[0045] Put the solution ① into the 2# reaction kettle, add 2 times the theoretical amount of iron powder, stir at room temperature for 1 hour, pour it into the filter, filter to obtain sponge copper and solution ②, the solution ② contains Zn 2+ 、Ni 2+ , Fe 2+ , Fe 3+ ;
[0046] Put the solution ② into the dissolution tank, use the aeration device to aerate with oxygen for 5 hours, and the aeration volume is 3m 3 / h, the oxygen concentration is 22%, and utilize steam to heat solut...
Embodiment 3
[0051] Take 1000kg of electroplating sludge (hereinafter referred to as solid waste, its main components are Cu, Ni, Zn, Ca, Fe) produced by a certain factory, put the electroplating sludge into 1# reactor, add 10wt% concentrated sulfuric acid 2.5t , normal temperature, after fully stirring for 2 hours, the leaching is completed, the solution is put into a filter press, filtered and separated to obtain calcium sulfate product and solution ①, solution ① contains Zn 2+ 、Cu 2+ 、Ni 2 + , Fe 2+ , Fe 3+ ;
[0052] Pour the solution ① into the 2# reaction kettle, add 3 times the theoretical amount of iron powder, stir at room temperature for 1 hour, pour it into the filter, filter to obtain sponge copper and solution ②, the solution ② contains Zn 2+ 、Ni 2+ , Fe 2+ , Fe 3+ ;
[0053] Put the solution ② into the dissolution tank, use the aeration device to aerate with oxygen for 6 hours, and the aeration volume is 4m 3 / h, the oxygen concentration is 24%, and utilize steam to...
PUM
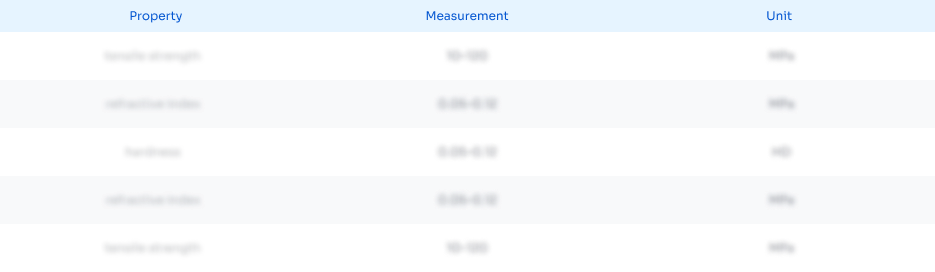
Abstract
Description
Claims
Application Information

- Generate Ideas
- Intellectual Property
- Life Sciences
- Materials
- Tech Scout
- Unparalleled Data Quality
- Higher Quality Content
- 60% Fewer Hallucinations
Browse by: Latest US Patents, China's latest patents, Technical Efficacy Thesaurus, Application Domain, Technology Topic, Popular Technical Reports.
© 2025 PatSnap. All rights reserved.Legal|Privacy policy|Modern Slavery Act Transparency Statement|Sitemap|About US| Contact US: help@patsnap.com