Manufacturing technique for stainless steel tubes used for hydraulic pipelines
A technology of stainless steel pipes and hydraulic pipes, applied in the direction of metal material coating process, manufacturing tools, furnace types, etc., can solve problems such as pipe rupture and oil leakage
- Summary
- Abstract
- Description
- Claims
- Application Information
AI Technical Summary
Problems solved by technology
Method used
Image
Examples
Embodiment 1
[0031] combine figure 1 , the production process of a stainless steel pipe for hydraulic pipelines involved in this embodiment, follows the steps in turn,
[0032] Step A: Heating the stainless steel tube blank, and performing heating, piercing and heading on a direct current frequency conversion piercing machine, the heating temperature is 1400° C., and kept for 20 minutes.
[0033] Step B, carry out the first pickling to the stainless steel pipe after step A treatment, and carry out grinding and lubricating; Potassium acid 20g / L, the rest is deionized water, the pickling temperature is 45°C, and the pickling time is 20 minutes.
[0034] Step C, cold-drawing the stainless steel pipe treated in step B to the required diameter and wall thickness.
[0035] Step D, carry out degreasing treatment to the stainless steel tube after step C treatment; The degreasing solution used in the degreasing treatment contains sodium hydroxide, sodium bicarbonate, sodium phosphate, sodium sili...
Embodiment 2
[0063] combine figure 1 , the production process of a stainless steel pipe for hydraulic pipelines involved in this embodiment, follows the steps in turn,
[0064] Step A: Heating the stainless steel tube blank, and performing heating, piercing and heading on a DC frequency conversion piercer, the heating temperature is 1200° C., and kept for 30 minutes.
[0065] Step B, carry out the first pickling to the stainless steel pipe after step A treatment, and carry out grinding and lubricating; Potassium acid potassium 50g / L, the rest is deionized water, the pickling temperature is 55°C, and the pickling time is 10 minutes.
[0066] Step C, cold-drawing the stainless steel pipe treated in step B to the required diameter and wall thickness.
[0067] Step D, degreasing the stainless steel pipe after the step C treatment; the degreasing solution used in the degreasing treatment contains sodium hydroxide, sodium bicarbonate, sodium phosphate, sodium silicate; the mass percentage of s...
PUM
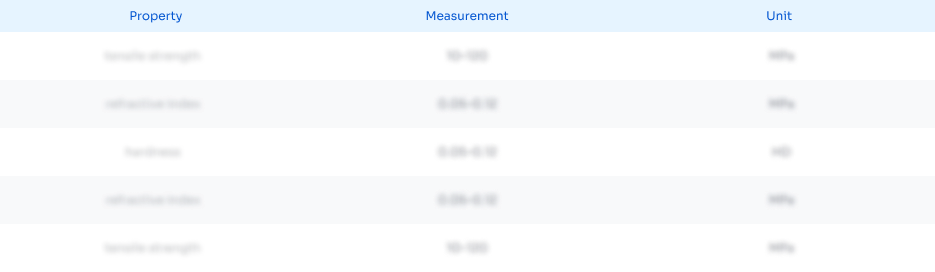
Abstract
Description
Claims
Application Information

- Generate Ideas
- Intellectual Property
- Life Sciences
- Materials
- Tech Scout
- Unparalleled Data Quality
- Higher Quality Content
- 60% Fewer Hallucinations
Browse by: Latest US Patents, China's latest patents, Technical Efficacy Thesaurus, Application Domain, Technology Topic, Popular Technical Reports.
© 2025 PatSnap. All rights reserved.Legal|Privacy policy|Modern Slavery Act Transparency Statement|Sitemap|About US| Contact US: help@patsnap.com