Reactive dye resist printing process based on ink jet printing process
A reactive dye and printing technology, applied in dyeing, textile and papermaking, etc., can solve the problems of unclean fabrics, soil color contamination, poor water holding capacity, etc. Simple to use effects
- Summary
- Abstract
- Description
- Claims
- Application Information
AI Technical Summary
Problems solved by technology
Method used
Image
Examples
Embodiment 1
[0024] A reactive dye resist printing process based on inkjet printing technology, comprising the following steps: sizing → drying → computer printing color separation and drawing (CAD) editing processing → adjusting anti-dye ink and spray printing → dyeing ground color → steaming → washing drying.
[0025] (1) Sizing treatment: the prescription of sizing agent is: 30% sodium alginate paste, 30% hydroxypropyl guar gum, 5% dispersant, 5% anti-swimming agent.
[0026] (2) Drying: Dry the sizing-treated fabric at 80° C. to 60% dry.
[0027] (3) Computer printing color separation and drawing (CAD) editing processing: through drawing and editing processing, the desired pattern is obtained, and then the inkjet nozzle is controlled by the computer.
[0028] (4) Optimizing the preparation of anti-dyeing reactive blue ink and printing formula: reactive dye 10%, triethylene glycol 6%, 1,4-butanediol 12%, N,N-dimethylformamide 6%, fatty alcohol 8% polyoxyethylene ether; 6% urea, 1% sod...
Embodiment 2
[0043] A reactive dye resist printing process based on inkjet printing technology, comprising the following steps: sizing→drying→computer printing color separation and drawing (CAD) editing processing→whitening ink and spray printing→ground color dyeing→steaming→washing drying.
[0044] (1) Sizing treatment: the prescription of sizing agent is: 35% sodium alginate paste, 4% dispersant, 3% anti-swimming agent, 23% deionized water.
[0045] (2) Drying: Dry the sizing-treated fabric at 80° C. to 60% dry.
[0046] (3) Computer printing color separation and drawing (CAD) editing processing: through drawing and editing processing, the desired pattern is obtained, and then the inkjet nozzle is controlled by the computer.
[0047](4) Preparation and printing of anti-white active ink: white paint 15%, triethylene glycol 6%, 1,4-butanediol 12%, N,N-dimethylformamide 6%, fatty alcohol polyoxyethylene Ether 8%; urea 6%, sodium dodecylbenzene sulfonate 1%, sodium benzoate 0.5%, triethano...
PUM
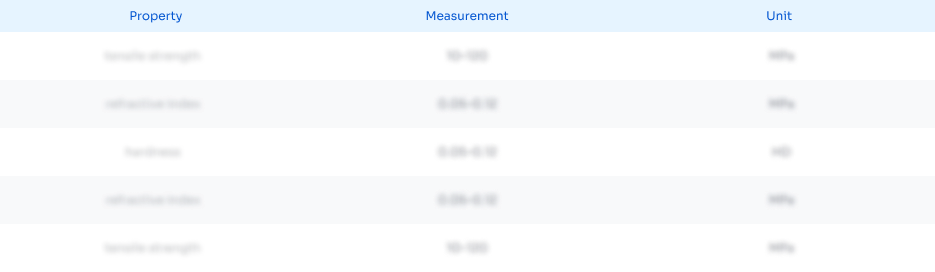
Abstract
Description
Claims
Application Information

- Generate Ideas
- Intellectual Property
- Life Sciences
- Materials
- Tech Scout
- Unparalleled Data Quality
- Higher Quality Content
- 60% Fewer Hallucinations
Browse by: Latest US Patents, China's latest patents, Technical Efficacy Thesaurus, Application Domain, Technology Topic, Popular Technical Reports.
© 2025 PatSnap. All rights reserved.Legal|Privacy policy|Modern Slavery Act Transparency Statement|Sitemap|About US| Contact US: help@patsnap.com