Self-repairing paint and preparation method thereof
A self-repairing and coating technology, which is applied in the direction of anti-corrosion coatings, epoxy resin coatings, coatings, etc., can solve problems such as poor repair effect, and achieve large load capacity, load capacity corrosion inhibitor release-response, and good repair ability Effect
- Summary
- Abstract
- Description
- Claims
- Application Information
AI Technical Summary
Problems solved by technology
Method used
Examples
example 1
[0025] Take 0.75g of cetyltrimethylammonium bromide, add 300mL of deionized water and mix evenly, then add 3.0mL of 8% sodium hydroxide solution, stir at 400r / min at 80°C for 2h, and then Add 4.0mL tetraethyl orthosilicate dropwise at 0.2mL / min, keep stirring at 600r / min for 2h, filter to obtain the precursor, wash the precursor with 5% hydrochloric acid for 5 times to obtain the pretreated precursor; take 0.75g pretreated Treat the precursor, add 7.5mL of 37% hydrochloric acid to 150mL of isopropanol, incubate at 65°C for 5 hours, filter to obtain a filter cake, wash the filter cake with deionized water and methanol for 8 times, and wash the washed The filter cake was placed in a vacuum drying oven and dried to constant weight at 40°C to obtain mesoporous silica nanospheres; take 0.75 g of mesoporous silica nanospheres and add 15 mL of 12% benzotriazole In the ethanol solution, under 50kPa, stir at 600r / min for 3h, then put it in a vacuum box and let it stand for 2h, then cen...
example 2
[0027]Take 0.50g of cetyltrimethylammonium bromide, add 200mL of deionized water and mix evenly, then add 1.5mL of 8% sodium hydroxide solution, stir at 300r / min at 70°C for 1h, and then Add 2.5mL tetraethyl orthosilicate dropwise at 0.1mL / min, keep stirring at 500r / min for 1h, filter to obtain the precursor, wash the precursor with 5% hydrochloric acid for 3 times to obtain the pretreated precursor; take 0.50g of pretreated Treat the precursor, add 5.0mL of 37% hydrochloric acid into 100mL of isopropanol, incubate at 60°C for 4 hours, filter to obtain a filter cake, wash the filter cake with deionized water and methanol for 5 times, and wash the washed The filter cake was placed in a vacuum drying oven and dried to constant weight at 30°C to obtain mesoporous silica nanospheres; take 0.50 g of mesoporous silica nanospheres and add 10 mL of 12% benzotriazole In the ethanol solution, under 10kPa, stir at 500r / min for 2h, then put it in a vacuum box and let it stand for 1h, then...
example 3
[0029] Take 0.65g of cetyltrimethylammonium bromide, add 250mL of deionized water and mix evenly, then add 2.5mL of 8% sodium hydroxide solution, stir at 350r / min at 75°C for 2h, and then Add 3.0mL tetraethyl orthosilicate dropwise at 0.1mL / min, keep stirring at 550r / min for 1h, filter to obtain the precursor, wash the precursor with 5% hydrochloric acid for 4 times to obtain the pretreated precursor; take 0.62g of pretreated Treat the precursor, add 6.5mL of 37% hydrochloric acid into 130mL of isopropanol, incubate at 62°C for 4 hours, filter to obtain a filter cake, wash the filter cake with deionized water and methanol for 7 times, and then wash the washed The filter cake was placed in a vacuum drying oven and dried to constant weight at 35°C to obtain mesoporous silica nanospheres; take 0.62g of mesoporous silica nanospheres and add 12mL of 12% benzotriazole In the ethanol solution, under 40kPa, stir at 550r / min for 2h, then put it in a vacuum box and let it stand for 1h, ...
PUM
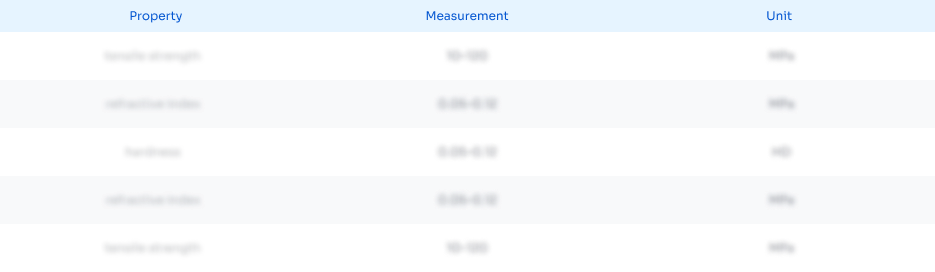
Abstract
Description
Claims
Application Information

- R&D
- Intellectual Property
- Life Sciences
- Materials
- Tech Scout
- Unparalleled Data Quality
- Higher Quality Content
- 60% Fewer Hallucinations
Browse by: Latest US Patents, China's latest patents, Technical Efficacy Thesaurus, Application Domain, Technology Topic, Popular Technical Reports.
© 2025 PatSnap. All rights reserved.Legal|Privacy policy|Modern Slavery Act Transparency Statement|Sitemap|About US| Contact US: help@patsnap.com