Application of integral type electrothermal wire mesh catalyst in catalytic combustion of volatile organic waste gas
A volatile organic and metal mesh technology, applied in the direction of metal/metal oxide/metal hydroxide catalyst, physical/chemical process catalyst, combustion method, etc., can solve the problems of high energy consumption and low energy utilization rate, Achieve the effects of low energy consumption, high energy utilization rate, and simple preparation method
- Summary
- Abstract
- Description
- Claims
- Application Information
AI Technical Summary
Problems solved by technology
Method used
Image
Examples
Embodiment 1
[0022] Surface pretreatment of iron-chromium-aluminum wire (wherein chromium: 23-26%, aluminum: 4.5-6.5%, and the rest is iron): take a certain length of wire and roll it into a spiral shape. Put the metal wire in acetone, ultrasonic for 30min, and rinse with distilled water. Then place the metal wire in 10wt% NaOH solution for 30min and rinse it with distilled water. Finally put the wire in 10wt% HNO 3 Sonicate the solution for 30 min, rinse with distilled water, and dry at 110°C for 2 h.
[0023] Preparation of FeCrAl wire surface coating: put the wire mesh in a pure oxygen atmosphere, and calcined at 950°C for 3h.
[0024] Preparation of noble metal Pd nanoparticles: Weigh 0.0176g palladium chloride, add 3mL oleylamine and 1mL oleic acid, under nitrogen atmosphere, magnetically stir, react at 180°C for 3h. After cooling to room temperature, transfer to a centrifuge tube. Add 3 times the volume of absolute ethanol, centrifuge (6000rpm, 5min), and precipitate, repeat the ...
Embodiment 2
[0028] Surface pretreatment of iron-chromium-aluminum wire (wherein chromium: 23-26%, aluminum: 4.5-6.5%, and the rest is iron): take a certain length of wire and roll it into a spiral shape. Put the metal wire in acetone, ultrasonic for 30min, and rinse with distilled water. Then place the metal wire in 10wt% NaOH solution for 30min and rinse it with distilled water. Finally put the wire in 10wt% HNO 3 Sonicate the solution for 30 min, rinse with distilled water, and dry at 110°C for 2 h.
[0029] Preparation of FeCrAl wire surface coating: put the wire mesh in a pure oxygen atmosphere, and calcined at 950°C for 3h.
[0030] Preparation of noble metal Pd nanoparticles: Weigh 0.0352g palladium chloride, add 6mL oleylamine and 2mL oleic acid, stir magnetically under nitrogen atmosphere, and react at 180°C for 3h. After cooling to room temperature, transfer to a centrifuge tube. Add 3 times the volume of absolute ethanol, centrifuge (6000rpm, 5min), and precipitate, repeat t...
Embodiment 3
[0034]Surface pretreatment of iron-chromium-aluminum wire (wherein chromium: 23-26%, aluminum: 4.5-6.5%, and the rest is iron): take a certain length of wire and roll it into a spiral shape. Put the metal wire in acetone, ultrasonic for 30min, and rinse with distilled water. Then place the metal wire in 10wt% NaOH solution for 30min and rinse it with distilled water. Finally put the wire in 10wt% HNO 3 Sonicate the solution for 30 min, rinse with distilled water, and dry at 110°C for 2 h.
[0035] Preparation of FeCrAl wire surface coating: put the wire mesh in a pure oxygen atmosphere, and calcined at 950°C for 3h.
[0036] Preparation of noble metal Pd nanoparticles: Weigh 0.0704g palladium chloride, add 12mL oleylamine and 4mL oleic acid, under nitrogen atmosphere, magnetically stir, react at 180°C for 3h. After cooling to room temperature, transfer to a centrifuge tube. Add 3 times the volume of absolute ethanol, centrifuge (6000rpm, 5min), and precipitate, repeat the ...
PUM
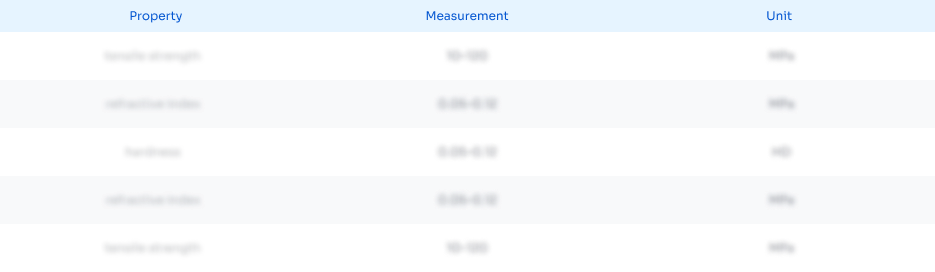
Abstract
Description
Claims
Application Information

- R&D
- Intellectual Property
- Life Sciences
- Materials
- Tech Scout
- Unparalleled Data Quality
- Higher Quality Content
- 60% Fewer Hallucinations
Browse by: Latest US Patents, China's latest patents, Technical Efficacy Thesaurus, Application Domain, Technology Topic, Popular Technical Reports.
© 2025 PatSnap. All rights reserved.Legal|Privacy policy|Modern Slavery Act Transparency Statement|Sitemap|About US| Contact US: help@patsnap.com