Modified epoxy vinyl resin for low-shrinkage concrete and preparation method thereof
A technology of epoxy vinyl resin and epoxy resin, which is applied in the field of concrete, can solve the problems of low shrinkage, sticky surface layer, stability and poor weather resistance, so as to improve weather resistance, increase filling rate and reduce curing shrinkage rate effect
- Summary
- Abstract
- Description
- Claims
- Application Information
AI Technical Summary
Problems solved by technology
Method used
Image
Examples
Embodiment example 1
[0063] 1) Preparation of modified epoxy resin
[0064] Weigh hydrogenated epoxy resin and bisphenol A epoxy resin in proportion (hydrogenated bisphenol A epoxy resin: bisphenol A diglycidyl ether=1:2, mass component ratio, 15 parts in total), join in Heat the reaction kettle to 100°C, and add catalyst A (0.01 parts of sodium titanate) and part of the crosslinking agent (8 parts of styrene) according to the mass components at the same time, control the pH value of the reaction system to 7.6, and fully react under this condition 20 minutes;
[0065] 2) Preparation of modified epoxy vinyl resin
[0066] The reaction temperature of the modified epoxy epoxy resin reaction kettle of step 1 is continuously cooled and the control temperature is 55°C, and the polymerization inhibitor (0.05 part of hydroquinone), initiator (0.01 part of triphenylsilanol-aluminum ethyl triacetoacetate), catalyst B (0.01 parts triphenylphosphine hydrogen), low shrinkage agent (2 parts polyvinyl acetate)...
Embodiment example 2
[0068] 1) Preparation of modified epoxy resin
[0069] Weigh hydrogenated epoxy resin and bisphenol A epoxy resin in proportion (hydrogenated bisphenol A epoxy resin: bisphenol A diglycidyl ether=1:2, mass component ratio, 22 parts in total), join in Heat the reaction kettle to 100°C, and at the same time add catalyst A (0.18 parts of sodium titanate) and part of the crosslinking agent (12 parts of styrene) according to the mass components, and control the pH value of the reaction system to 8.0, and fully react under this condition 25 minutes;
[0070] 2) Preparation of modified epoxy vinyl resin
[0071] The reaction temperature of the modified epoxy epoxy resin reaction kettle of step 1 is continuously cooled and the control temperature is 70°C, and the polymerization inhibitor (0.08 part of hydroquinone), initiator (0.03 part of triphenylsilanol-triacetoacetate aluminum), catalyst B (0.08 parts of triphenylphosphine hydrogen), low shrinkage agent (5 parts of polyvinyl ace...
Embodiment example 3
[0073] 1) Preparation of modified epoxy resin
[0074] Weigh hydrogenated epoxy resin and bisphenol A epoxy resin in proportion (hydrogenated bisphenol A epoxy resin: bisphenol A diglycidyl ether=1:2, mass component ratio, 32 parts in total), join in Heat the reaction kettle to 100°C, and simultaneously add catalyst A (0.5 parts of sodium titanate) and part of the crosslinking agent (12 parts of styrene) according to the mass components, and control the pH value of the reaction system to 8.8, and fully react under this condition 30 minutes;
[0075] 2) Preparation of modified epoxy vinyl resin
[0076] The reaction temperature of the modified epoxy epoxy resin reaction kettle of step 1 is continuously cooled and the control temperature is 80°C, and the polymerization inhibitor (0.08 part of hydroquinone), initiator (0.05 part of triphenylsilanol-triacetoacetate ethyl aluminum), catalyst B (0.1 part of triphenylphosphine hydrogen), low shrinkage agent (8 parts of polyvinyl ac...
PUM
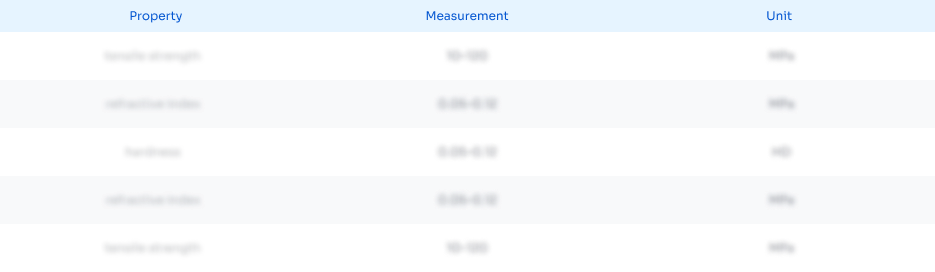
Abstract
Description
Claims
Application Information

- R&D Engineer
- R&D Manager
- IP Professional
- Industry Leading Data Capabilities
- Powerful AI technology
- Patent DNA Extraction
Browse by: Latest US Patents, China's latest patents, Technical Efficacy Thesaurus, Application Domain, Technology Topic, Popular Technical Reports.
© 2024 PatSnap. All rights reserved.Legal|Privacy policy|Modern Slavery Act Transparency Statement|Sitemap|About US| Contact US: help@patsnap.com