Processing method of special-shaped deep groove for titanium alloy parts
A processing method and titanium alloy technology, which is applied in the field of special-shaped deep groove processing of titanium alloy parts, can solve the problems of large damage to CNC tools, poor processing quality, and low processing efficiency, so as to improve surface quality, reduce feed rate, and improve The effect of processing efficiency
- Summary
- Abstract
- Description
- Claims
- Application Information
AI Technical Summary
Problems solved by technology
Method used
Image
Examples
Embodiment Construction
[0033] The embodiments of the present invention will be described in detail below with reference to the accompanying drawings, but the present invention can be implemented in various ways defined and covered below.
[0034] figure 1 It is a flow chart of the steps of the method for machining a special-shaped deep groove of a titanium alloy part in a preferred embodiment of the present invention; figure 2 It is a schematic diagram of the structure of the drill bit subjected to axial force in the preferred embodiment of the present invention; image 3 It is a schematic diagram of the outline of the special-shaped deep groove of the titanium alloy part of the preferred embodiment of the present invention; Figure 4 It is a schematic diagram of corner drilling in a preferred embodiment of the present invention; Figure 5 It is a schematic diagram of corner fine boring in a preferred embodiment of the present invention; Image 6 It is a schematic diagram of corner reaming in a ...
PUM
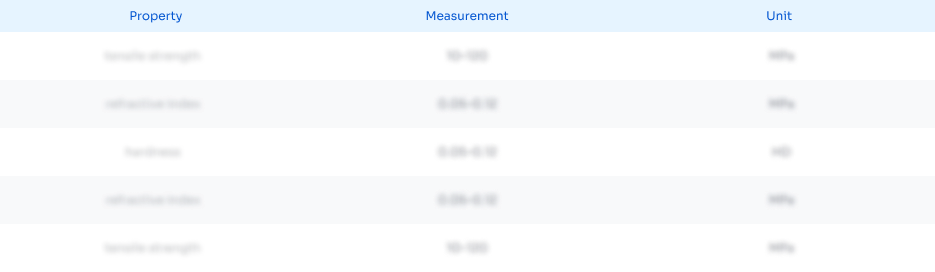
Abstract
Description
Claims
Application Information

- Generate Ideas
- Intellectual Property
- Life Sciences
- Materials
- Tech Scout
- Unparalleled Data Quality
- Higher Quality Content
- 60% Fewer Hallucinations
Browse by: Latest US Patents, China's latest patents, Technical Efficacy Thesaurus, Application Domain, Technology Topic, Popular Technical Reports.
© 2025 PatSnap. All rights reserved.Legal|Privacy policy|Modern Slavery Act Transparency Statement|Sitemap|About US| Contact US: help@patsnap.com