Preparation method of magnesium sulfate monohydrate
A technology of magnesium sulfate heptahydrate and magnesium sulfate, applied in the direction of magnesium sulfate, energy input, etc., can solve the problems of low content of sulfur-containing magnesium in magnesium sulfate heptahydrate, long-term storage of products, easy agglomeration, and difficult mixing, so as to save equipment Good investment and commercial effect, good energy saving effect
- Summary
- Abstract
- Description
- Claims
- Application Information
AI Technical Summary
Problems solved by technology
Method used
Image
Examples
Embodiment 1
[0025] A preparation method for magnesium sulfate monohydrate, comprising the following steps:
[0026] (1) drop the magnesium sulfate heptahydrate containing surface water 3wt%~12wt% in the vibrating fluidized bed;
[0027] (2) Continuously feed the high-temperature flue gas generated in the sintering process into the vibrating fluidized bed described in step (1) to dry the wet material; control the flue gas flow rate in the drier to u≥2.5m / s, The temperature of the flue gas is 180°C. At this time, magnesium sulfate heptahydrate absorbs the heat of the flue gas and then dries to generate magnesium sulfate monohydrate;
[0028] (3) collect magnesium sulfate monohydrate from the outlet of vibrating fluidized bed.
[0029] (4) Carry out tail gas treatment step again, specifically:
[0030] After drying and using the exhaust gas, the fine powder materials brought out of the exhaust gas are recovered by the dust collector, and collected into the bag of the dust collector to red...
Embodiment 2
[0032] A preparation method for magnesium sulfate monohydrate, comprising the following steps:
[0033] (1) drop the magnesium sulfate heptahydrate containing surface water 3wt%~12wt% in the rotary kiln;
[0034] (2) Continuously feed the high-temperature flue gas generated in the sintering process into the vibrating fluidized bed described in step (1) to dry the wet material; control the flue gas flow rate in the drier to u≥2.5m / s, The temperature of the flue gas was 120°C. At this time, magnesium sulfate heptahydrate absorbs the heat of the flue gas and then dries to generate magnesium sulfate monohydrate;
[0035] (3) Collect magnesium sulfate monohydrate from the outlet of rotary kiln.
[0036] (4) Carry out tail gas treatment step again, specifically:
[0037] After drying and using the exhaust gas, the fine powder materials brought out of the exhaust gas are recovered by the dust collector, and collected into the bag of the dust collector to reduce the loss of fine po...
Embodiment 3
[0039] A preparation method for magnesium sulfate monohydrate, comprising the following steps:
[0040] (1) drop the magnesium sulfate heptahydrate containing surface water 3wt%~12wt% in the vibrating fluidized bed;
[0041] (2) Continuously feed the high-temperature flue gas generated in the pelletizing process into the vibrating fluidized bed described in step (1) to dry the wet material; control the flue gas flow rate inside the dryer u ≥ 2.5m / s , the temperature of the flue gas is 160°C, at this time, magnesium sulfate heptahydrate absorbs the heat of the flue gas and dries to generate magnesium sulfate monohydrate;
[0042] (3) collect magnesium sulfate monohydrate from the outlet of vibrating fluidized bed.
[0043] (4) Carry out tail gas treatment step again, specifically:
[0044] After drying and using the exhaust gas, the fine powder materials brought out of the exhaust gas are recovered by the dust collector, and collected into the bag of the dust collector to red...
PUM
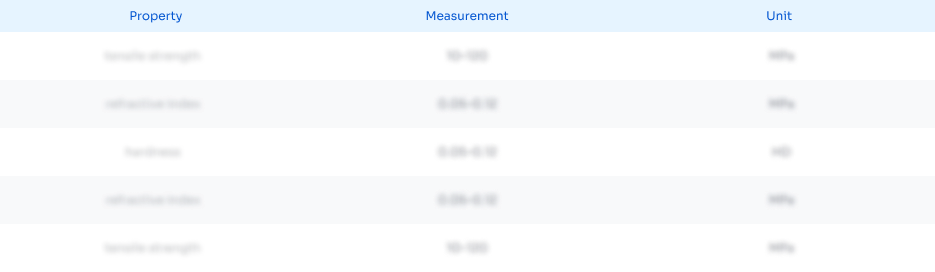
Abstract
Description
Claims
Application Information

- R&D
- Intellectual Property
- Life Sciences
- Materials
- Tech Scout
- Unparalleled Data Quality
- Higher Quality Content
- 60% Fewer Hallucinations
Browse by: Latest US Patents, China's latest patents, Technical Efficacy Thesaurus, Application Domain, Technology Topic, Popular Technical Reports.
© 2025 PatSnap. All rights reserved.Legal|Privacy policy|Modern Slavery Act Transparency Statement|Sitemap|About US| Contact US: help@patsnap.com