A method for producing chlorinated paraffin-52 by combining thermal chlorination and photocatalysis
A chlorinated paraffin and photocatalysis technology, applied in petrochemical modification and other directions, can solve the problems of uneven distribution of chlorine gas, low chlorine gas conversion rate, uneven ultraviolet light irradiation, etc., to shorten the reaction time, save energy costs, Even heating effect
- Summary
- Abstract
- Description
- Claims
- Application Information
AI Technical Summary
Problems solved by technology
Method used
Image
Examples
Embodiment 1
[0029] A method for producing chlorinated paraffin-52 in combination with thermal chlorination and photocatalysis, comprising the following steps:
[0030] 1) Prepare a filter screen 2, the filter screen 2 is composed of the following materials in parts by weight: 10 parts of carbon fiber, 20 parts of silica gel, 5 parts of polyurethane resin, and 1 part of seaweed particles;
[0031] 2) Melt the solid paraffin and flow through the filter screen 2 to obtain refined liquid paraffin;
[0032] 3) described refining liquid paraffin is passed into reactor 5 that is added with catalyzer; Described catalyzer is 0.1% of solid paraffin weight;
[0033] 4) The reactor 5 is rotated along the horizontal axis, and the refined liquid paraffin and the catalyst are mixed for 10 min at a temperature of 80° C.;
[0034] 5) Feed chlorine gas into the position of the horizontal axis where the reactor 5 rotates, keep the reactor rotating along the horizontal axis, use a black light lamp 6 to irra...
Embodiment 2
[0042] A method for producing chlorinated paraffin-52 in combination with thermal chlorination and photocatalysis, comprising the following steps:
[0043] 1) Prepare a filter screen 2, the filter screen 2 is composed of the following materials in parts by weight: 15 parts of carbon fiber, 40 parts of silica gel, 10 parts of polyurethane resin, and 5 parts of seaweed particles;
[0044] 2) Melting the solid paraffin and flowing through the filter screen 2 to obtain refined liquid paraffin;
[0045] 3) said refined liquid paraffin is passed into the reactor 5 that is added with catalyzer; Said catalyzer is 0.2% of solid paraffin weight;
[0046] 4) Rotating the reactor 5 along the horizontal axis, mixing the refined liquid paraffin and the catalyst at a temperature of 100° C. for 10 minutes;
[0047] 5) Feed chlorine gas into the position of the horizontal axis where the reactor 5 rotates, keep the reactor rotating along the horizontal axis, use a black light lamp 6 to irradia...
Embodiment 3
[0055] A method for producing chlorinated paraffin-52 in combination with thermal chlorination and photocatalysis, comprising the following steps:
[0056] 1) Prepare a filter screen 2, the filter screen 2 is composed of the following materials in parts by weight: 12 parts of carbon fiber, 30 parts of silica gel, 8 parts of polyurethane resin, and 3 parts of seaweed particles;
[0057] 2) Melting the solid paraffin and flowing through the filter screen 2 to obtain refined liquid paraffin;
[0058] 3) said refined liquid paraffin is passed into the reactor 5 that is added with catalyzer; Said catalyzer is 0.2% of solid paraffin weight;
[0059] 4) The reactor 5 is rotated along the horizontal axis, and the refined liquid paraffin and the catalyst are mixed for 8 minutes at a temperature of 90° C.;
[0060] 5) Feed chlorine gas into the position of the horizontal axis where the reactor 5 rotates, keep the reactor rotating along the horizontal axis, irradiate the reactor with a ...
PUM
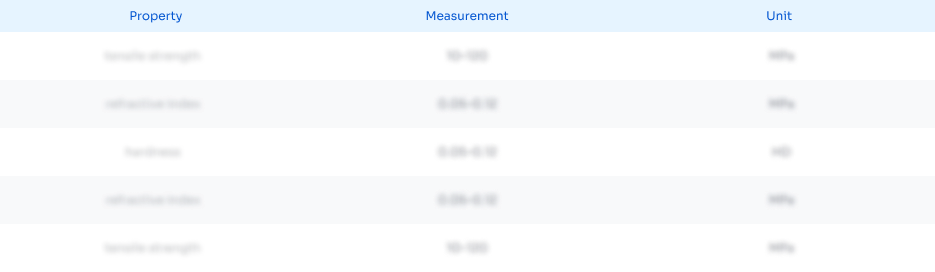
Abstract
Description
Claims
Application Information

- Generate Ideas
- Intellectual Property
- Life Sciences
- Materials
- Tech Scout
- Unparalleled Data Quality
- Higher Quality Content
- 60% Fewer Hallucinations
Browse by: Latest US Patents, China's latest patents, Technical Efficacy Thesaurus, Application Domain, Technology Topic, Popular Technical Reports.
© 2025 PatSnap. All rights reserved.Legal|Privacy policy|Modern Slavery Act Transparency Statement|Sitemap|About US| Contact US: help@patsnap.com