Tantalum sputtering target, and production method therefor
The technology of sputtering target and diffraction method is applied in the field of tantalum sputtering target, which can solve the problems of high film formation speed and uncontrollable film thickness uniformity, and achieve the effect of excellent film thickness uniformity.
- Summary
- Abstract
- Description
- Claims
- Application Information
AI Technical Summary
Problems solved by technology
Method used
Image
Examples
Embodiment 1
[0046] A tantalum raw material with a purity of 99.997% was electron beam melted and cast to produce an ingot with a length of 1000 mm and a diameter of 195 mmφ. Next, this ingot was subjected to cold press forging to have a diameter of 150 mm, and then cut to a required length to obtain a billet. Next, heat treatment was performed at a temperature of 1250°C, cold forging was performed once again, heat treatment was performed at 1000°C, followed by secondary cold forging, divided into 2 parts, and heat treatment was performed again at 1000°C.
[0047] Next, cold rolling is performed on the forged billet. For the rolling process, the continuous rolling passes with a reduction ratio of less than 6% were repeated 30 times in total, and then rolling was performed in the rolling passes with a reduction ratio of 6% or more. After rolling, it is heat treated at 800°C. Next, a tantalum sputtering target with a thickness of 6.35 mm and 450 mmφ was produced by machining the obtained t...
Embodiment 2-5
[0050] A forged billet was produced by the same method as in Example 1 or the like. Next, cold rolling is performed on the forged billet. In the rolling process, as shown in Table 1, the total number of continuous rolling passes with a reduction ratio of less than 6% is adjusted, and then rolling is carried out with a rolling pass with a reduction ratio of 6% or more, so that the total reduction ratio Reach more than 85%. After rolling, heat treatment is performed at 800°C. Next, a tantalum sputtering target with a thickness of 6.35 mm and 450 mmφ was produced by machining the obtained target material with a thickness of 10 mm and 500 mmφ.
[0051] About the sputtering target obtained by the above process, the structure of the cross section perpendicular|vertical to the sputtering surface of a target was observed using the method similar to Example 1. As a result, the area ratios of crystal grains in which the {100} planes were oriented along the ND were all 30% or more. M...
PUM
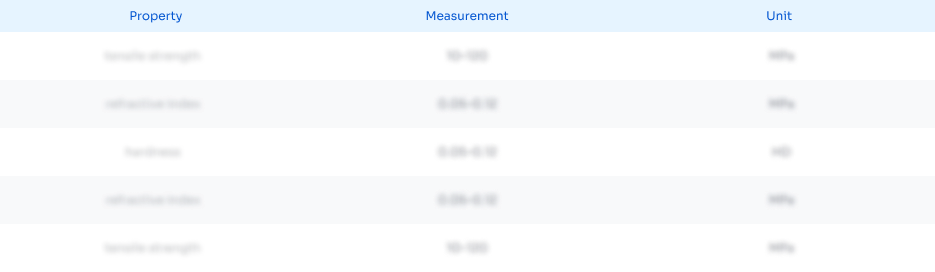
Abstract
Description
Claims
Application Information

- R&D Engineer
- R&D Manager
- IP Professional
- Industry Leading Data Capabilities
- Powerful AI technology
- Patent DNA Extraction
Browse by: Latest US Patents, China's latest patents, Technical Efficacy Thesaurus, Application Domain, Technology Topic, Popular Technical Reports.
© 2024 PatSnap. All rights reserved.Legal|Privacy policy|Modern Slavery Act Transparency Statement|Sitemap|About US| Contact US: help@patsnap.com