Method for acquiring main energy source required by supercritical carbon dioxide power generation in cement plant
A technology of carbon dioxide and acquisition method, applied in the fields of environmental protection and energy
- Summary
- Abstract
- Description
- Claims
- Application Information
AI Technical Summary
Problems solved by technology
Method used
Image
Examples
Embodiment 1
[0068] A method adapted to the supercritical CO 2 Method for generating the required energy: Built-in CO in the kiln hood 2 The energy storage device directly stores the strong radiant heat energy in the kiln hood of the dry process rotary kiln production line at a normal temperature of 800°C to 1450°C and higher, and uses the stored high-temperature heat energy to convert CO 2 Conversion to high-energy-density high-pressure thermal supercritical CO 2 fluid, as supercritical CO 2 The main energy source for power generation.
[0069] The kiln hood built-in CO 2 energy storage devices, such as Figure 1a-Figure 1b As shown, it mainly includes kiln head cover 1, CO 2 Fluid energy storage mechanism 2, hanger 3, check valve 4, regulating valve 5, safety valve 6 and temperature and pressure sensor 7, the CO 2 The fluid energy storage mechanism 2 includes a disc-type hollow tube heat exchanger 2a and a box-type heat exchanger 2c. The disc-type hollow tube heat exchanger 2a is f...
Embodiment 2
[0072] In order to solve the unfavorable effects of high-temperature hot clinker sintering and making snowmen in the grate cooler of the cement plant, it is obtained and adapted to supercritical CO 2 Method to generate energy required for power generation: Built-in CO with a grate cooler 2 The energy storage device directly stores the strong radiation / conduction heat energy of the clinker in the grate cooler of the dry-process rotary kiln production line at 200°C to 1350°C, and uses the stored high-temperature heat energy to convert CO 2 Conversion to high-energy-density high-pressure thermal supercritical CO 2 Fluid energy, as supercritical CO 2 the primary energy source for power generation;
[0073] The grate cooler built-in CO 2 energy storage devices, such as Figure 2a-Figure 2b As shown, it mainly includes grate cooler 8, CO 2 Fluid energy storage mechanism 2, hanger 3, check valve 4, regulating valve 5, safety valve 6 and temperature and pressure sensor 7, the CO ...
Embodiment 3
[0076] A kind of supercritical CO 2 Method of generating energy required for power generation: Built-in CO in the kiln tail smoke chamber 2 The energy storage device directly stores the high-temperature radiation / conduction heat energy in the kiln tail smoke chamber of the cement production line at 850°C to 1200°C, and uses the stored high-temperature heat energy to convert CO 2 Conversion to high-energy-density high-pressure thermal supercritical CO 2 Fluid energy, as supercritical CO 2 The energy generated by the generating set;
[0077] The kiln tail smoke chamber built-in CO 2 energy storage devices, such as image 3 As shown, it mainly includes kiln tail smoke chamber 9, CO 2 Fluid energy storage mechanism 2, hanger 3, check valve 4, regulating valve 5, safety valve 6 and temperature and pressure sensor 7, the CO 2 The fluid energy storage mechanism 2 includes a disc-type hollow tube heat exchanger 2a and a plate-type heat exchanger 2b, and the disc-type hollow tube...
PUM
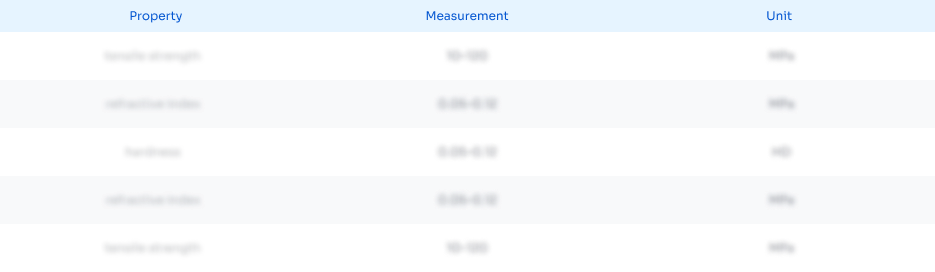
Abstract
Description
Claims
Application Information

- R&D
- Intellectual Property
- Life Sciences
- Materials
- Tech Scout
- Unparalleled Data Quality
- Higher Quality Content
- 60% Fewer Hallucinations
Browse by: Latest US Patents, China's latest patents, Technical Efficacy Thesaurus, Application Domain, Technology Topic, Popular Technical Reports.
© 2025 PatSnap. All rights reserved.Legal|Privacy policy|Modern Slavery Act Transparency Statement|Sitemap|About US| Contact US: help@patsnap.com