Method for preparing nano-calcium carbonate powder through high-energy ball milling
A nano-calcium carbonate powder, high-energy ball milling technology, applied in the direction of calcium carbonate/strontium/barium, nanotechnology, etc., can solve the problems such as unseen preparation, and achieve the effects of easy industrial production, large output and low cost
- Summary
- Abstract
- Description
- Claims
- Application Information
AI Technical Summary
Problems solved by technology
Method used
Image
Examples
Embodiment 1
[0039] 1. Weigh calcium chloride and sodium carbonate powder at a molar ratio of 1:2, and weigh 30 g of grinding balls so that the ball-to-material ratio is 20:1;
[0040] 2. Add the mixture in 1 into the ball mill tank, set the ball mill time to 60 min, set the ball mill speed to 300rpm, 600rpm, 900rpm and 1000rpm in turn, and start the ball mill;
[0041] 3. After the reaction time is over, take out the white powder in the ball mill tank and dry it in an electric heating constant temperature blast drying oven for 5 hours. Finally, the white powder is stored in a centrifuge tube for subsequent detection. Carry out XRD detection to the obtained product, such as figure 1 As shown, the result shows that when the ball milling speed is 300rpm, the reactant calcium chloride and sodium carbonate react substantially completely, and the product has obvious diffraction peaks of sodium chloride, but there is no diffraction peak of calcite; when the ball milling speed increases to 600rp...
Embodiment 2
[0044] 1. Weigh calcium chloride and sodium carbonate powder at a molar ratio of 1:1.5, and weigh 15 g of grinding balls so that the ball-to-material ratio is 5:1, 10:1, 20:1, and 30:1, respectively;
[0045] 2 Add the mixture in 1 into the ball mill tank, set the ball mill speed to 1000rpm, set the ball mill time to 30min, 60min, 120min and 180min in sequence, and start the ball mill;
[0046] 3. After the reaction time is over, take out the white powder in the ball mill jar, and dry it in an electric constant temperature blast drying oven for 6 hours. Finally, the white powder is stored in a centrifuge tube for subsequent detection. Carry out XRD detection to the obtained product, such as image 3 As shown, the longitudinal comparison results show that increasing the ball-to-material ratio (from 5:1 to 30:1), the reactants calcium chloride and sodium carbonate change from unreacted to completely reacted, and the diffraction peak of calcite appears and becomes more and more ...
Embodiment 3
[0049] 1. Weigh calcium chloride and sodium carbonate powder according to the molar ratio of 1:1, and then weigh 15 g, 30 g, 45 g and 60 g of grinding balls respectively, so that the ball-to-material ratio is 20:1 and 30:1 respectively;
[0050] 2. Add the mixture in 1 into the ball mill tank, set the ball mill speed to 900rpm, set the ball mill time to 60 min and 120 min in turn, and start the ball mill;
[0051] 3. After the reaction time is over, take out the white powder in the ball mill jar and dry it in an electric constant temperature blast drying oven for 7 hours. Finally, the white powder is stored in a centrifuge tube for subsequent detection. Carry out XRD detection to the obtained product, such as Figure 5 As shown, the vertical comparison results show that the diffraction peak of calcite disappears gradually when the mass of the ball increases (from 15 g to 60 g); the horizontal comparison results show that the diffraction peak of calcite Emerge and become sharp...
PUM
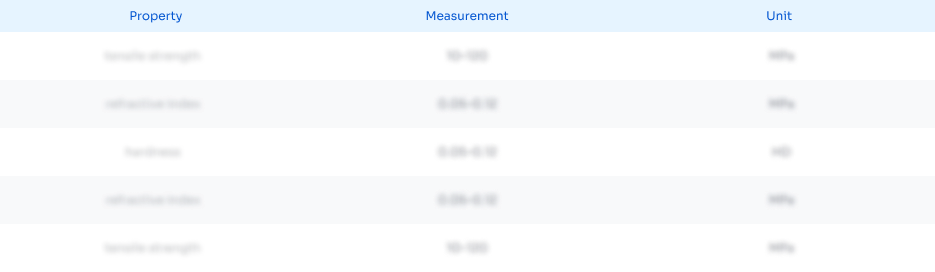
Abstract
Description
Claims
Application Information

- Generate Ideas
- Intellectual Property
- Life Sciences
- Materials
- Tech Scout
- Unparalleled Data Quality
- Higher Quality Content
- 60% Fewer Hallucinations
Browse by: Latest US Patents, China's latest patents, Technical Efficacy Thesaurus, Application Domain, Technology Topic, Popular Technical Reports.
© 2025 PatSnap. All rights reserved.Legal|Privacy policy|Modern Slavery Act Transparency Statement|Sitemap|About US| Contact US: help@patsnap.com