Composite laminated friction stir welding additive forming process for large thick-walled cylindrical parts
A friction stir welding and friction stir technology, applied in welding equipment, manufacturing tools, non-electric welding equipment, etc., can solve the problems of low production efficiency, serious energy consumption and slow solidification speed.
- Summary
- Abstract
- Description
- Claims
- Application Information
AI Technical Summary
Problems solved by technology
Method used
Image
Examples
Embodiment Construction
[0029] The present invention will be described in detail below in conjunction with the accompanying drawings.
[0030] refer to Figure 1 to Figure 7 , a composite laminated friction stir welding additive forming process for large thick-walled cylindrical parts, characterized in that it includes the following steps:
[0031] 1) Single rolling forming of thin-walled ring parts: use radial-axial hot rolling technology to make thin-walled ring parts, and prepare metal ingots to prepare friction stir welding through blanking, billet making, ring rolling, heat treatment and machining processes. Thin-walled ring monomers required for additive forming;
[0032]2) Thin-walled ring single piece radially stacked friction stir welding additive forming: first, the first thin-walled ring single piece 1a and the second thin-walled ring single piece 1b are fixed on the welding table in the form of coaxial radial stacking butt joint As the workpiece to be welded; then, the welding wire 6 is...
PUM
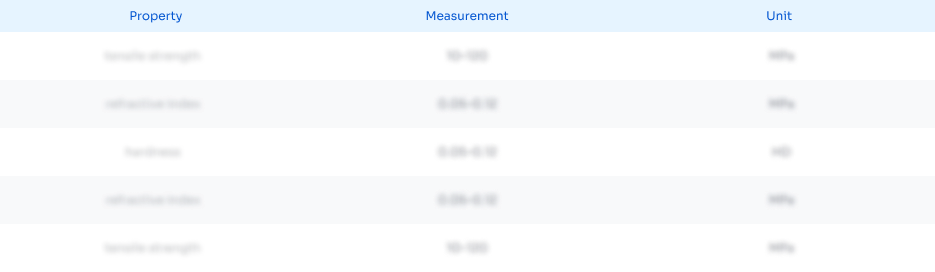
Abstract
Description
Claims
Application Information

- R&D
- Intellectual Property
- Life Sciences
- Materials
- Tech Scout
- Unparalleled Data Quality
- Higher Quality Content
- 60% Fewer Hallucinations
Browse by: Latest US Patents, China's latest patents, Technical Efficacy Thesaurus, Application Domain, Technology Topic, Popular Technical Reports.
© 2025 PatSnap. All rights reserved.Legal|Privacy policy|Modern Slavery Act Transparency Statement|Sitemap|About US| Contact US: help@patsnap.com