Tellurobismuthite leaching method
A bismuth telluride ore and leaching technology, applied in the field of metallurgy, can solve the problems of incomplete processing of raw materials, few sources, low product output and the like
- Summary
- Abstract
- Description
- Claims
- Application Information
AI Technical Summary
Problems solved by technology
Method used
Examples
Embodiment 1
[0017] Leach tellurium from gray bismuthite: the original gray bismuthite contains 3.65% tellurium and 4.89% bismuth, and the grinding particle size reaches 90% ore powder is over 200 mesh. Put the above-mentioned bismuth tellurite into a roasting furnace, and roast at a temperature of 400°C for 5 hours. Continue to grind the fully roasted ore powder until 90% of the ore powder passes 200 mesh. Slowly add the pretreated bismuth tellurite to a 180g / L sulfuric acid solution at a solid-to-liquid ratio = 1:4, pass through an ozone concentration of 30mg / h, add 0.8g sodium dodecylbenzenesulfonate powder, and For leaching, the leaching process adopts 150r / min mechanical stirring, and the leaching stirring time is 3h. The measured and calculated tellurium content in the leaching solution is 98.78%, and the bismuth content is 97.23%.
Embodiment 2
[0019] Leach tellurium from gray bismuthite: the original gray bismuthite contains 3.02% tellurium and 7.78% bismuth, and the grinding particle size reaches 90% ore powder is over 200 mesh. Put the above-mentioned bismuth tellurite into a roasting furnace, and roast at a temperature of 400°C for 5 hours. Continue to grind the fully roasted ore powder until 90% of the ore powder passes 200 mesh. Slowly add the pretreated bismuth tellurite to a 180g / L sulfuric acid solution at a solid-to-liquid ratio = 1:4, pass through an ozone concentration of 30mg / h, add 0.8g sodium dodecylbenzenesulfonate powder, and For leaching, the leaching process adopts 150r / min mechanical stirring, and the leaching stirring time is 3h. The measured and calculated tellurium content in the leaching solution is 99.02%, and the bismuth content is 98.65%.
Embodiment 3
[0021] Leach tellurium from gray bismuthite: the original gray bismuthite contains 3.20% tellurium and 5.92% bismuth, and the grinding particle size reaches 90% ore powder is over 200 mesh. Put the above-mentioned bismuth tellurite into a roasting furnace, and roast at a temperature of 400°C for 5 hours. Continue to grind the fully roasted ore powder until 90% of the ore powder passes 200 mesh. Slowly add the pretreated bismuth tellurite to a 180g / L sulfuric acid solution at a solid-to-liquid ratio = 1:4, pass through an ozone concentration of 30mg / h, add 0.8g sodium dodecylbenzenesulfonate powder, and For leaching, the leaching process adopts 150r / min mechanical stirring, and the leaching stirring time is 3h. The measured and calculated tellurium content in the leaching solution is 98.31%, and the bismuth content is 97.11%.
PUM
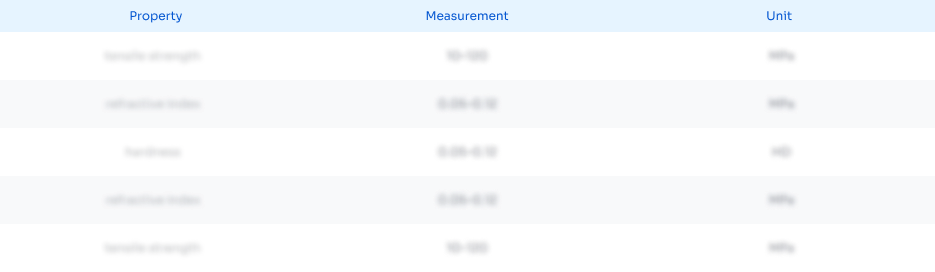
Abstract
Description
Claims
Application Information

- R&D
- Intellectual Property
- Life Sciences
- Materials
- Tech Scout
- Unparalleled Data Quality
- Higher Quality Content
- 60% Fewer Hallucinations
Browse by: Latest US Patents, China's latest patents, Technical Efficacy Thesaurus, Application Domain, Technology Topic, Popular Technical Reports.
© 2025 PatSnap. All rights reserved.Legal|Privacy policy|Modern Slavery Act Transparency Statement|Sitemap|About US| Contact US: help@patsnap.com