Polymer/intercalation montmorillonite composite fluid loss reducer and its preparation method and application
A fluid loss reducer and polymer technology, applied in the field of oil and gas well cementing, can solve the problems of inability to resist calcium and magnesium ions, inability to carry out construction, thickening of cement slurry, etc., and achieve strong resistance to calcium and magnesium ion pollution and easy control. , The effect of strong water loss performance
- Summary
- Abstract
- Description
- Claims
- Application Information
AI Technical Summary
Problems solved by technology
Method used
Image
Examples
Embodiment 1
[0045] Put 4.5g of montmorillonite, 0.2g of octadecyltrimethylammonium bromide and 78g of distilled water into a 250mL four-necked flask, mix and stir for 12 hours, add 3.2g of sodium hydroxide, 0.3g of tributyl phosphate, and 0.02g Sodium methacrylic acid sulfonate, 0.01g ethylenediaminetetraacetic acid, 16.4g 2-acrylamido-2-methylpropanesulfonic acid, 1.9g N,N-dimethylacrylamide, 0.3g maleic anhydride, stir 2 hours, fill the solution with nitrogen for 40 minutes, start heating to 50°C, then add 0.12g ammonium persulfate, and continue to heat up to 70°C, add 0.02g p-hydroxyanisole after 3 hours, and finally get light red or light Yellow viscous liquid.
Embodiment 2
[0047] Add 3g montmorillonite, 0.2g cetyltrimethylammonium bromide and 78g distilled water into a 250mL four-neck flask, mix and stir for 12 hours, add 2.5g potassium hydroxide, 0.3g tributyl phosphate and 0.02g benzene Sodium ethylene sulfonate, 0.01g disodium ethylenediaminetetraacetic acid, 12.8g 2-acrylamido-2-methylpropanesulfonic acid, 3.4g N,N-diethylacrylamide, 0.56g fumaric anhydride, stir 2 hours, fill the solution with nitrogen for 40 minutes, start heating to 55°C, then add 0.21g sodium persulfate, and continue to heat up to 75°C, add 0.02g hydroquinone after 3 hours, and finally get light red or light yellow Viscous liquid.
Embodiment 3
[0049] Add 4g montmorillonite, 0.2g hexadecyldimethylammonium bromide and 78g distilled water into a 250mL four-neck flask, mix and stir for 12 hours, add 2.5g potassium hydroxide, 0.3g emulsified silicone oil, 0.02g thioglycolic acid , 0.01g ethylenediaminetetraacetic acid, 12.8g methacrylic acid, 3.4g N,N-diethylacrylamide, 0.56g fumaric anhydride, stir for 2 hours, inflate the solution with nitrogen for 40 minutes, start heating to 50℃ , Then add 0.21g potassium persulfate, and continue to heat up to 70 ℃, after 3 hours, finally get a light red or light yellow viscous liquid.
PUM
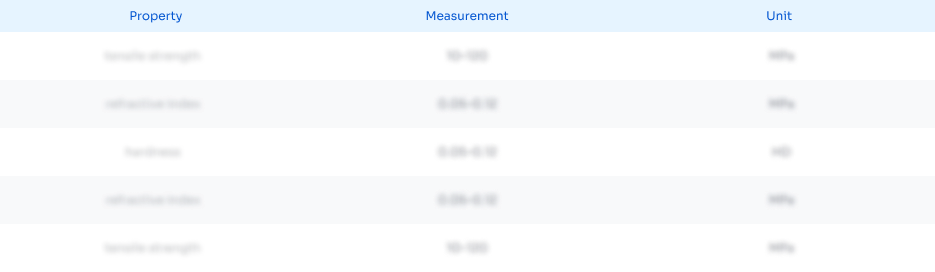
Abstract
Description
Claims
Application Information

- Generate Ideas
- Intellectual Property
- Life Sciences
- Materials
- Tech Scout
- Unparalleled Data Quality
- Higher Quality Content
- 60% Fewer Hallucinations
Browse by: Latest US Patents, China's latest patents, Technical Efficacy Thesaurus, Application Domain, Technology Topic, Popular Technical Reports.
© 2025 PatSnap. All rights reserved.Legal|Privacy policy|Modern Slavery Act Transparency Statement|Sitemap|About US| Contact US: help@patsnap.com