Method and system for treating vanadium extraction tailings
A technology for extracting vanadium tailings and vanadium slag, which is applied to the improvement of process efficiency, photography technology, instruments, etc., and can solve the problem of low utilization rate of vanadium extraction tailings
- Summary
- Abstract
- Description
- Claims
- Application Information
AI Technical Summary
Problems solved by technology
Method used
Image
Examples
Embodiment 1
[0084] Vanadium extraction tailings (TFe content 30wt%, V 2 o 5 content of 1 wt%, Ga content of 0.010 wt%) and reduced coal according to the mass ratio of 100:15 for mixed molding treatment to obtain mixed pellets. The mixed pellets were reduced and roasted to obtain metallized pellets. The roasting temperature was 1200° C. for 30 minutes, and the metallization rate of the metallized pellets was 90%. Metallized pellets are subjected to grinding and magnetic separation to obtain gallium-containing iron powder (containing gallium 0.030wt%) and vanadium-rich slag (V 2 o 5 Content 2wt%). The vanadium-rich slag and sodium salt are mixed according to the mass ratio of 100:10, and then sodium oxide is roasted in an air atmosphere to obtain water-soluble sodium vanadate clinker (the proportion of pentavalent vanadium to total vanadium is 92%), and sodium oxide is The roasting temperature is 600°C, the time is 2h, and the water-soluble sodium vanadate clinker is soaked in water-pur...
Embodiment 2
[0086] Vanadium extraction tailings (TFe content 35wt%, V 2 o 5 content of 2wt%, Ga content of 0.012wt%) and reduced coal in a mass ratio of 100:20 for mixed molding treatment to obtain mixed pellets. The mixed pellets were reduced and roasted to obtain metallized pellets. The roasting temperature was 1300° C. for 60 minutes, and the metallization rate of the metallized pellets was 92%. Metallized pellets are subjected to grinding and magnetic separation to obtain gallium-containing iron powder (containing gallium 0.036wt%) and vanadium-rich slag (V 2 o 5 Content 4wt%). The vanadium-rich slag and sodium salt are mixed according to the mass ratio of 100:20, and then sodium oxide is roasted in an air atmosphere to obtain water-soluble sodium vanadate clinker (the proportion of pentavalent vanadium to total vanadium is 94%), and sodium oxide is The roasting temperature is 700°C, the time is 1.5h, and the water-soluble sodium vanadate clinker is soaked in water-purified-precip...
Embodiment 3
[0088] Vanadium extraction tailings (TFe content 40wt%, V 2 o 5 content of 4wt%, Ga content of 0.015wt%) and reduced coal in a mass ratio of 100:25 for mixed molding treatment to obtain mixed pellets. The mixed pellets were reduced and roasted to obtain metallized pellets. The roasting temperature was 1400° C. for 90 minutes, and the metallization rate of the metallized pellets was 95%. Metallized pellets are subjected to grinding and magnetic separation to obtain gallium-containing iron powder (containing gallium 0.045wt%) and vanadium-rich slag (V 2 o 5 Content 8wt%). The vanadium-rich slag and sodium salt are mixed according to the mass ratio of 100:30, and then sodium oxide is roasted in an air atmosphere to obtain water-soluble sodium vanadate clinker (the proportion of pentavalent vanadium to total vanadium is 96%), and sodium oxide is The roasting temperature is 900°C, the time is 1h, and the water-soluble sodium vanadate clinker is soaked in water-purified-vanadium...
PUM
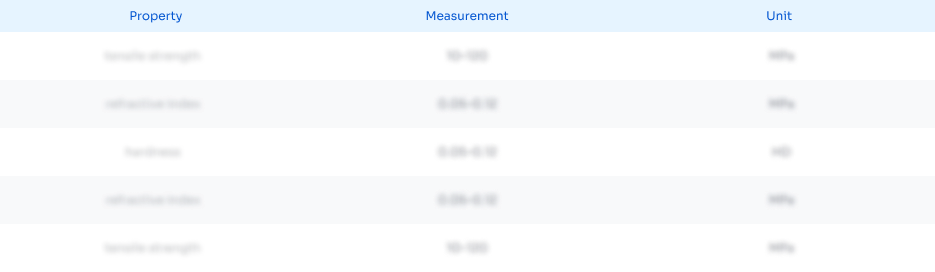
Abstract
Description
Claims
Application Information

- R&D
- Intellectual Property
- Life Sciences
- Materials
- Tech Scout
- Unparalleled Data Quality
- Higher Quality Content
- 60% Fewer Hallucinations
Browse by: Latest US Patents, China's latest patents, Technical Efficacy Thesaurus, Application Domain, Technology Topic, Popular Technical Reports.
© 2025 PatSnap. All rights reserved.Legal|Privacy policy|Modern Slavery Act Transparency Statement|Sitemap|About US| Contact US: help@patsnap.com