Anti-pollution composite membrane, and making method and oil-water emulsion separation method thereof
A composite membrane, anti-pollution technology, applied in semi-permeable membrane separation, chemical instruments and methods, permeation/dialysis water/sewage treatment, etc., to achieve high anti-pollution performance, simple manufacturing process, and improve the effect of permeate water flux
- Summary
- Abstract
- Description
- Claims
- Application Information
AI Technical Summary
Problems solved by technology
Method used
Image
Examples
preparation example Construction
[0035]The preparation method of the pollution-resistant composite membrane is also disclosed in the embodiment. Taking the hollow fiber sulfonated or aminated polymer-coated composite nanofiltration membrane as an example, it is prepared by the following steps: dissolving the sulfonated or aminated polymer in solvent, prepare a coating solution; then apply the coating solution to the inner surface of the nanofiltration base membrane to obtain a composite membrane; heat-treat the obtained composite membrane in an environment of 50-70°C for 5-10 hours, and dry Finally, a sulfonated or aminated polymer-coated composite nanofiltration membrane is obtained.
[0036] Wherein, the mass percent concentration of the sulfonated or aminated polymer in the coating solution is 0.01-10%, preferably 0.5-10%. The sulfonated polymer is selected from sulfonated polyether ether ketone, sulfonated polystyrene, sulfonated polyaniline, sulfonated polysulfone; or the aminated polymer is selected fro...
Embodiment 1
[0052] Dissolving sulfonated polyetheretherketone in methanol solution to prepare a solution with a sulfonated polymer concentration of 0.01%. Apply it to the PVDF flat base membrane (inner and outer diameters are 0.9mm and 1.4mm respectively) with a single coating, and treat the membrane for 6 hours in an environment of 65 degrees Celsius to obtain a composite membrane with an effective coating (that is, an effective separation layer) , the effective coating thickness of the sulfonated polyether ether ketone composite nanofiltration membrane is 0.01 μm, and the nanofiltration membrane is assembled into a hollow fiber membrane module and used as attached figure 1 The process shown is for degreasing.
[0053] The raw material liquid is oily wastewater, and sodium dodecylsulfonate is added to obtain stable emulsified oil. Here and in the following several examples, the synthetic emulsified oil used in the experiment is adopted, and the main component of the waste water itself i...
Embodiment 2
[0055] Dissolve sulfonated polyethersulfone in methanol solution to prepare a coating solution with a high molecular concentration of 5.0%, and coat it on the PES flat base film (the base film MWCO is 100000Da, the ratio of internal and external diameters is 0.9 / 1.3mm), 65 degrees The membrane was post-treated for 6 hours in the environment to obtain a composite membrane. The effective coating thickness of the sulfonated polyether ether ketone composite nanofiltration membrane was 1 μm. figure 1 Degreasing is carried out in the process shown.
[0056] The raw material liquid is oily wastewater, and sodium hexadecylsulfonate is added to obtain stable emulsified oil. During the operation, adjust the pressure pump and valve to make the pressure reach 6bar. The oil content in the permeated water cannot be detected, which meets the first-level discharge standard of the "Integrated Wastewater Discharge Standard" (GB8978-1996). During the operation of the device, the permeate water...
PUM
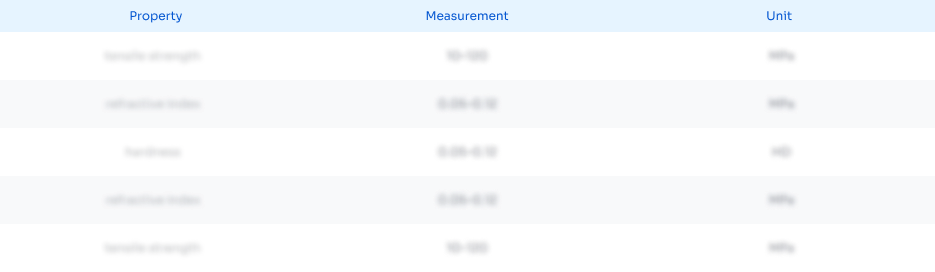
Abstract
Description
Claims
Application Information

- R&D
- Intellectual Property
- Life Sciences
- Materials
- Tech Scout
- Unparalleled Data Quality
- Higher Quality Content
- 60% Fewer Hallucinations
Browse by: Latest US Patents, China's latest patents, Technical Efficacy Thesaurus, Application Domain, Technology Topic, Popular Technical Reports.
© 2025 PatSnap. All rights reserved.Legal|Privacy policy|Modern Slavery Act Transparency Statement|Sitemap|About US| Contact US: help@patsnap.com