Composite with high compressive strength and preparation method of composite
A technology of compressive strength and composite materials, applied in the direction of manufacturing tools, ceramic molding machines, etc., can solve the problems of low tensile strength, buildings cannot reach the quality level, poor thermal insulation performance, etc., and achieve compressive strength and bonding strength. High, suitable for large-scale industrial application, good thermal insulation effect
- Summary
- Abstract
- Description
- Claims
- Application Information
AI Technical Summary
Problems solved by technology
Method used
Examples
Embodiment 1
[0024] (1) Accurately weigh 35 parts of Portland cement, 30 parts of perlite, 28 parts of hydroxyethyl cellulose ether, 25 parts of ceramic powder, 18 parts of vermiculite, 12 parts of polytetrafluoroethylene, laurel 10 parts of dimethyl amine oxide, 8 parts of triethanolamine, 6 parts of o-hydroxymethylbenzoic acid lactone, 6 parts of aluminum silicate high temperature cotton, 4 parts of polypropylene fiber, 2 parts of hydrogenated castor oil, 2 parts of zinc stearate 3 parts, 3 parts of aluminum dihydrogen phosphate, 3 parts of fatty alcohol polyoxyethylene ether, 150 parts of distilled water;
[0025] (2) Put Portland cement, perlite, ceramic powder, vermiculite, and zinc stearate together in a planetary ball mill for ball milling. The speed of the ball mill is 220 r / min, and the ball milling time is 1 h. 250 mesh sieves to obtain preliminary mixture;
[0026] (3) Put hydroxyethyl cellulose ether, lauryl dimethyl amine oxide, triethanolamine, and o-hydroxymethylbenzoic aci...
Embodiment 2
[0031] (1) Accurately weigh 40 parts of Portland cement, 35 parts of perlite, 30 parts of hydroxyethyl cellulose ether, 30 parts of ceramic powder, 19 parts of vermiculite, 14 parts of polytetrafluoroethylene, laurel 13 parts of dimethyl amine oxide, 9 parts of triethanolamine, 7 parts of o-hydroxymethylbenzoic acid lactone, 7 parts of aluminum silicate high temperature cotton, 5 parts of polypropylene fiber, 3 parts of hydrogenated castor oil, 3 parts of zinc stearate 4 parts, 4 parts of ethylene propylene copolymer, 4 parts of polyacrylamide, 150 parts of distilled water;
[0032] (2) Put Portland cement, perlite, ceramic powder, vermiculite, and zinc stearate together in a planetary ball mill for ball milling. The speed of the ball mill is 250 r / min, and the ball milling time is 1.5 h. 300 mesh sieves to obtain preliminary mixture;
[0033] (3) Put hydroxyethyl cellulose ether, lauryl dimethyl amine oxide, triethanolamine, and o-hydroxymethylbenzoic acid lactone in a mixer...
Embodiment 3
[0038] (1) Accurately weigh 45 parts of Portland cement, 40 parts of perlite, 32 parts of hydroxyethyl cellulose ether, 35 parts of ceramic powder, 20 parts of vermiculite, 16 parts of polytetrafluoroethylene, laurel 15 parts of dimethyl amine oxide, 10 parts of triethanolamine, 8 parts of o-hydroxymethylbenzoic acid lactone, 8 parts of aluminum silicate high temperature cotton, 6 parts of polypropylene fiber, 4 parts of hydrogenated castor oil, 4 parts of zinc stearate 5 parts of urea-formaldehyde resin, 5 parts of methyl silicone oil, 150 parts of distilled water;
[0039] (2) Put Portland cement, perlite, ceramic powder, vermiculite, and zinc stearate together in a planetary ball mill for ball milling. The speed of the ball mill is 280 r / min, and the ball milling time is 2 h. 350 mesh sieves to obtain preliminary mixture;
[0040] (3) Put hydroxyethyl cellulose ether, lauryl dimethyl amine oxide, triethanolamine, and o-hydroxymethylbenzoic acid lactone in a mixer for stirr...
PUM
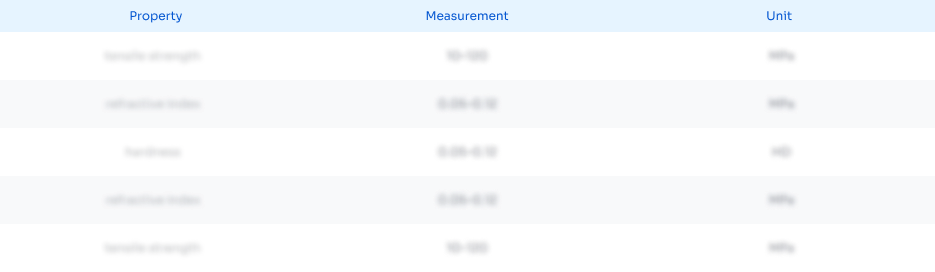
Abstract
Description
Claims
Application Information

- Generate Ideas
- Intellectual Property
- Life Sciences
- Materials
- Tech Scout
- Unparalleled Data Quality
- Higher Quality Content
- 60% Fewer Hallucinations
Browse by: Latest US Patents, China's latest patents, Technical Efficacy Thesaurus, Application Domain, Technology Topic, Popular Technical Reports.
© 2025 PatSnap. All rights reserved.Legal|Privacy policy|Modern Slavery Act Transparency Statement|Sitemap|About US| Contact US: help@patsnap.com