Method and system for treating schreyerite
A vanadium-titanium ore grinding technology, applied in the field of metallurgy, can solve the problems of titanium resource loss, energy consumption, material consumption, high cost, difficulty in meeting high-efficiency, low-carbon, green production, etc.
- Summary
- Abstract
- Description
- Claims
- Application Information
AI Technical Summary
Problems solved by technology
Method used
Image
Examples
Embodiment 1
[0070] The raw ore is crushed and finely ground until the vanadium-titanium ore powder with a particle size of less than 75 μm accounts for about 50% by weight and sent to a magnetic separator for rough separation. , Table 2 and Table 3. During roughing, the magnetic field strength is 2000Oe. After roughing, the vanadium-titanium ore is transported to the mine through a belt, and the water is dried to 4% for use. After roughing, the vanadium-titanium ore powder is transported to the fluidized Bed silo, the furnace material is fed from the middle of the fluidized bed to the preheated fluidized bed through a screw feeder, and the iron ore is preheated to 400°C and sent to the oxidation roasting fluidized bed at a roasting temperature of 1100°C to oxidize the iron in the iron ore It is trivalent iron, destroys the phase structure of vanadium-titanium magnetite, iron-containing black titanite and magnesium-containing black titanite, and roasts for 30 minutes. The oxidized and roas...
Embodiment 2
[0085] The raw ore is crushed and finely ground until the vanadium-titanium ore powder with a particle size of less than 75 μm accounts for about 40% by weight and sent to a magnetic separator for rough separation. , Table 2 and Table 3. During roughing, the magnetic field strength is 1800Oe. The vanadium-titanium ore after roughing is transported to the mine through a belt, and the water is dried to 4% for use. The vanadium-titanium ore powder after roughing is transported to the fluidized bed silo, the furnace material is fed from the middle of the fluidized bed to the preheated fluidized bed through a screw feeder, and the vanadium-titanium ore powder is preheated to 400°C and sent to the oxidation roasting fluidized bed at a roasting temperature of 900°C. The iron in the ore is oxidized to ferric iron, which destroys the phase structure of vanadium-titanium magnetite, iron-containing black titanite and magnesium-containing black titanite. The roasting time is 30 minutes, a...
PUM
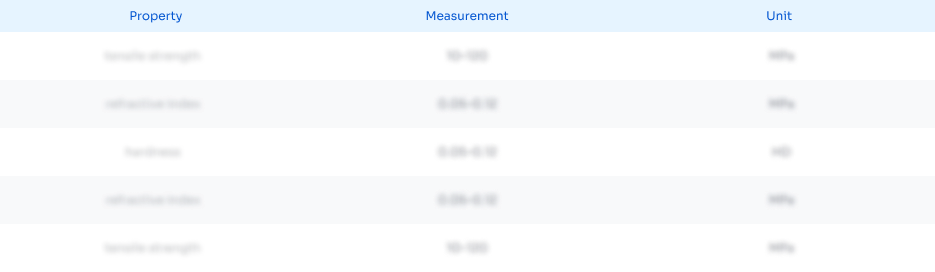
Abstract
Description
Claims
Application Information

- R&D
- Intellectual Property
- Life Sciences
- Materials
- Tech Scout
- Unparalleled Data Quality
- Higher Quality Content
- 60% Fewer Hallucinations
Browse by: Latest US Patents, China's latest patents, Technical Efficacy Thesaurus, Application Domain, Technology Topic, Popular Technical Reports.
© 2025 PatSnap. All rights reserved.Legal|Privacy policy|Modern Slavery Act Transparency Statement|Sitemap|About US| Contact US: help@patsnap.com