Magnesium alloy surface processing method and magnesium alloy
A treatment method and surface treatment technology, applied in the direction of surface reaction electrolytic coatings, coatings, electrolytic coatings, etc., can solve the problems of poor adhesion and corrosion resistance of colored films, and cannot obtain golden yellow effects, etc., and achieve good sensory effects , Improve use value and added value, high adhesion and corrosion resistance
- Summary
- Abstract
- Description
- Claims
- Application Information
AI Technical Summary
Problems solved by technology
Method used
Examples
Embodiment 1
[0053] (1) Preparation of micro-arc oxidation solution A1
[0054] Potassium hydroxide 2 g / L, sodium silicate 15 g / L, sodium fluoride 4 g / L, potassium carbonate 12 g / L and sodium benzoate 2 g / L were sequentially put into water. Stir continuously during the addition process, one reagent is completely dissolved, then add the next one, and stand for 1.5 hours after all the reagents are dissolved, to obtain the micro-arc oxidation solution of this embodiment, which is recorded as A1.
[0055] (2) Preparation of colorant B1
[0056] Ferric ammonium oxalate was dissolved in water to prepare an aqueous solution with a content of ferric ammonium oxalate of 12 g / L. After standing for 2 hours, the colorant B1 of this embodiment was obtained.
[0057] (3) Degreasing treatment
[0058] The magnesium alloy was immersed in sodium hydroxide with a concentration of 80 g / L for degreasing treatment at a temperature of 70 °C for 10 minutes.
[0059] (4) Micro-arc oxidation
[0060] Put the m...
Embodiment 2
[0066] (1) Preparation of micro-arc oxidation solution A2
[0067] Add 3 g / L of potassium hydroxide, 32 g / L of sodium silicate, 5 g / L of sodium fluoride, 15 g / L of potassium carbonate and 5 g / L of sodium benzoate into the water in sequence. Stir continuously during the addition process, one reagent is completely dissolved and then add the next one, and stand for 2 hours after all the reagents are dissolved to obtain the micro-arc oxidation solution of this embodiment, which is recorded as A2.
[0068] (2) Preparation of colorant B2
[0069] Ferric ammonium oxalate was dissolved in water to prepare an aqueous solution with a ferric ammonium oxalate content of 25 g / L, which was left to stand for 2 hours before use to obtain the colorant B2 of this embodiment.
[0070] (3) Degreasing treatment
[0071] The magnesium alloy was immersed in sodium hydroxide with a concentration of 100 g / L for degreasing treatment at a temperature of 80 °C for 20 minutes.
[0072] (4) Micro-arc ox...
Embodiment 3
[0079] (1) Preparation of micro-arc oxidation solution A3
[0080] Potassium hydroxide 5 g / L, sodium silicate 35 g / L, sodium fluoride 6 g / L, potassium carbonate 14 g / L and sodium benzoate 4 g / L were sequentially put into water. Stir continuously during the addition process, one reagent is completely dissolved before adding the next one, and after all the reagents are dissolved, stand for 2 hours and then use for later use to obtain the micro-arc oxidation solution of this embodiment, which is recorded as A3.
[0081] (2) Preparation of colorant B3
[0082] Ferric ammonium oxalate was dissolved in water to prepare an aqueous solution with a content of ferric ammonium oxalate of 15 g / L. After standing for 2 hours, the colorant B3 of this embodiment was obtained.
[0083] (3) Degreasing treatment
[0084] The magnesium alloy was immersed in sodium hydroxide with a concentration of 110 g / L for degreasing treatment at a temperature of 80°C for 15 minutes.
[0085] (4) Micro-arc ...
PUM
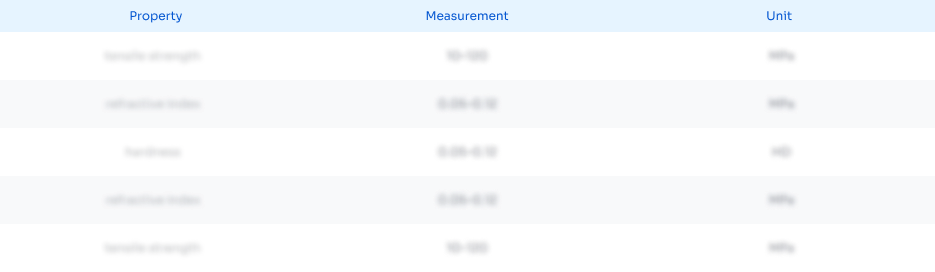
Abstract
Description
Claims
Application Information

- R&D Engineer
- R&D Manager
- IP Professional
- Industry Leading Data Capabilities
- Powerful AI technology
- Patent DNA Extraction
Browse by: Latest US Patents, China's latest patents, Technical Efficacy Thesaurus, Application Domain, Technology Topic, Popular Technical Reports.
© 2024 PatSnap. All rights reserved.Legal|Privacy policy|Modern Slavery Act Transparency Statement|Sitemap|About US| Contact US: help@patsnap.com