Preparation method of particle size controllable tin dioxide nano-powder
A nano-powder, tin dioxide technology, applied in tin oxide and other directions, to achieve the effects of short reaction period, low cost, and easy control of the reaction process
- Summary
- Abstract
- Description
- Claims
- Application Information
AI Technical Summary
Problems solved by technology
Method used
Image
Examples
Embodiment 1
[0029] Take 2.37g (0.02mol) of metal Sn grains, add it into a three-necked flask, and add 3.75ml of HNO2 dropwise to the flask 3 And 5ml HCl, and the deionized water of 8.75ml, the control reaction temperature is 80 ℃, and the reaction time is 2.5h, obtains the Sn ion solution, adds the ethanol solution of 3.53ml (equivalent to 0.2L / L) in the Sn ion solution, After adding, let stand for 12h. The above mixed solution and ammonia (25wt.%) solution were simultaneously titrated into 0.3wt.% PVA aqueous solution, the reaction temperature was controlled to be 65° C., the reaction time was 1 h, and the pH value was 3 to obtain a suspension. The suspension was left to stand for 12 hours, then filtered, washed three times with deionized water and absolute ethanol, then dried at 100°C for 5 hours, then ground and calcined at 600°C for 2 hours to obtain the final Tin oxide nanopowder.
Embodiment 2
[0031] Take 2.37g (0.02mol) of metal Sn grains, add it into a three-necked flask, and add 3.75ml of HNO2 dropwise to the flask 3 And 5ml HCl, and the deionized water of 8.75ml, control reaction temperature to be 80 ℃, reaction time is 2.5h, obtain Sn ion solution, add the HNO of 1.875ml (equivalent to 0.107L / L) in Sn ion solution 3solution, add 5.29ml (equivalent to 0.3L / L) ethanol solution to the Sn ion solution, and let stand for 12h after adding. The above mixed solution and ammonia (25wt.%) solution were simultaneously titrated into 0.3wt.% PVA aqueous solution, the reaction temperature was controlled to be 65° C., the reaction time was 1 h, and the pH value was 3 to obtain a suspension. The suspension was left to stand for 12 hours, then filtered, washed three times with deionized water and absolute ethanol, then dried at 100°C for 5 hours, then ground and calcined at 600°C for 2 hours to obtain the final Tin oxide nanopowder.
Embodiment 3
[0033] Take 2.37g (0.02mol) of metal Sn grains, add it into a three-necked flask, and add 3.75ml of HNO2 dropwise to the flask 3 And 5ml HCl, and the deionized water of 8.75ml, control reaction temperature to be 80 ℃, reaction time is 2.5h, obtain Sn ion solution, add the HNO of 3.75ml (equivalent to 0.215L / L) in Sn ion solution 3 solution, add 7.056ml (equivalent to 0.4L / L) ethanol solution to the Sn ion solution, and let stand for 12h after adding. The above mixed solution and ammonia (25wt.%) solution were simultaneously titrated into 0.3wt.% PVA aqueous solution, the reaction temperature was controlled to be 65° C., the reaction time was 1 h, and the pH value was 3 to obtain a suspension. The suspension was left to stand for 12 hours, then filtered, washed three times with deionized water and absolute ethanol, then dried at 100°C for 5 hours, then ground and calcined at 600°C for 2 hours to obtain the final Tin oxide nanopowder.
PUM
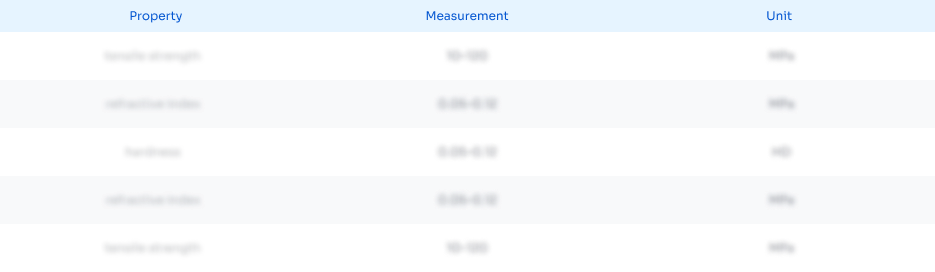
Abstract
Description
Claims
Application Information

- R&D
- Intellectual Property
- Life Sciences
- Materials
- Tech Scout
- Unparalleled Data Quality
- Higher Quality Content
- 60% Fewer Hallucinations
Browse by: Latest US Patents, China's latest patents, Technical Efficacy Thesaurus, Application Domain, Technology Topic, Popular Technical Reports.
© 2025 PatSnap. All rights reserved.Legal|Privacy policy|Modern Slavery Act Transparency Statement|Sitemap|About US| Contact US: help@patsnap.com