Ethylene oxide waste gas treatment and energy recovery system
A technology for waste gas treatment and energy recovery, which is applied in gas treatment, combustion methods, fixed tubular conduit assemblies, etc., and can solve problems such as high safety hazards, ethylene oxide discharge into the atmosphere, and environmental pollution.
- Summary
- Abstract
- Description
- Claims
- Application Information
AI Technical Summary
Problems solved by technology
Method used
Image
Examples
Embodiment
[0020] Example: refer to figure 1 with 2 . An ethylene oxide waste gas treatment and energy recovery system, comprising an ethylene oxide sterilizer 1, a tail gas absorption device 2, and an energy recovery device 3, the tail gas absorption device 2 including a water ring vacuum pump 21, a steam-water separator 22 , water storage tank 23, several combined ethylene glycol reaction tanks 25, combined spray tower 26; the upper side of the steam-water separator 22 is provided with a water inlet, the lower side is provided with a water outlet, the top is provided with an air outlet, and the bottom A drain port with a drain valve is provided, the EO waste gas outlet pipe of the ethylene oxide sterilizer 1 is connected to the inlet end of the water ring vacuum pump 21, and the gas-liquid mixing outlet end of the water ring vacuum pump 21 passes through the pipeline It is connected to the water inlet, and the water outlet is connected to the water return end on the top side of the w...
Embodiment 2
[0025] Embodiment 2: refer to image 3 . A number of fifth heat exchange tubes 37 are arranged in the central heating water tank 9, and one or more sets of air-water heat exchangers 32 are circularly connected with one side heat exchange interface of the corresponding combined air energy heat pump 33, one or more The heat exchange ports on the other side of the multiple sets of combined air source heat pumps 33 communicate with one or more sets of fifth heat exchange tubes 37 . Thus, the incinerated gas is heat-exchanged to the combined air-energy heat pump 33 through the air-water heat exchanger 32, and then transferred to the fifth heat-exchange tube 37 by the combined air-energy heat pump 33 to achieve heat exchange for the water in the central heating water tank 9. .
Embodiment 3
[0026] Embodiment 3: refer to Figure 1-3 . The ethylene oxide sterilizer processes the ethylene oxide waste gas produced by it. When sterilizing, the concentration of ethylene oxide in the cavity is about 650mg / L; the acid solution in the combined ethylene glycol reaction tank 25 passes through chemical circulation The pump is pressurized and transported to the top of the combined spray tower 26, and the acid liquid is sprayed onto the liquid uniform distributor through the acid liquid dispersing nozzle of the spray device 29. When working, ethylene oxide passes through the liquid distributor from bottom to top, and acid liquid passes through the liquid distributor from top to bottom, maximizing the contact surface area of ethylene oxide and acid, so that the ethylene oxide can be maximized Dissolved in the acid solution; when burning, the ethylene glycol waste liquid passes through the chemical high-pressure pump and the electric control valve to pass the ethylene glycol ...
PUM
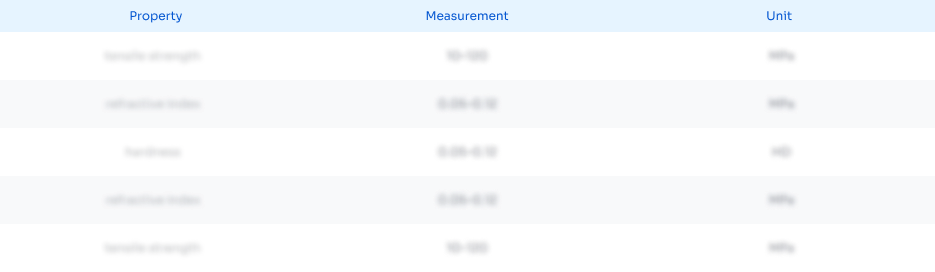
Abstract
Description
Claims
Application Information

- R&D
- Intellectual Property
- Life Sciences
- Materials
- Tech Scout
- Unparalleled Data Quality
- Higher Quality Content
- 60% Fewer Hallucinations
Browse by: Latest US Patents, China's latest patents, Technical Efficacy Thesaurus, Application Domain, Technology Topic, Popular Technical Reports.
© 2025 PatSnap. All rights reserved.Legal|Privacy policy|Modern Slavery Act Transparency Statement|Sitemap|About US| Contact US: help@patsnap.com