Preparation method of graphitized carbon negative electrode material
A technology of graphitized carbon and negative electrode materials, applied in the field of lithium ion batteries, can solve the problems of increased battery impedance, battery capacity loss, and large lithium ion diffusion resistance.
- Summary
- Abstract
- Description
- Claims
- Application Information
AI Technical Summary
Problems solved by technology
Method used
Image
Examples
preparation example Construction
[0030] The invention provides a method for preparing a graphitized carbon negative electrode material, comprising the following steps:
[0031] 1) Calcining the fatty acid at a temperature of 600-800° C. for 6-8 hours in a nitrogen atmosphere, and obtaining amorphous carbon after cooling;
[0032] 2) Calcining the amorphous carbon obtained in step 1) in a nitrogen atmosphere at a temperature of 2500-2800° C. for 4-6 hours, and cooling to obtain graphitized carbon;
[0033] 3) Dispersing the graphitized carbon obtained in step 2) and a certain amount of nitrogen-containing polymer in absolute ethanol, mixing evenly, spraying into balls to form a precursor, and then collecting the precursor through a cyclone separator;
[0034] 4) carbonizing the precursor obtained in step 3) in a nitrogen atmosphere at a temperature of 800-1000° C. for 2-4 hours, and obtaining porous graphitized carbon after cooling;
[0035] 5) Disperse the porous graphitized carbon obtained in step 4) and a ...
Embodiment 1
[0040] Weigh 8.5g of lauric acid and put it into a tube furnace, calcinate in a nitrogen atmosphere at a temperature of 600°C for 8h, and obtain amorphous carbon after cooling; then calcinate the amorphous carbon in a nitrogen atmosphere at a temperature of 2500°C for 6h , naturally cooled to room temperature to obtain graphitized carbon; then graphitized carbon and polypyrrole were dispersed in absolute ethanol according to a mass ratio of 1:1, and sprayed into balls after 0.5h of ultrasonic dispersion and 2h of magnetic stirring, wherein, The inlet temperature of the spray into balls is about 190°C, the outlet temperature is about 130°C, and then the precursor is collected by a cyclone separator; next, the precursor is carbonized in a nitrogen atmosphere at a temperature of 800°C for 4 hours, and porous graphitization is obtained after cooling Carbon: Finally, disperse 4g of porous graphitized carbon and 1g of sucrose in 50mL of deionized water, transfer them to a watch glass...
Embodiment 2
[0042] Weigh 9.0g of myristic acid and put it into a tube furnace, calcinate in a nitrogen atmosphere at a temperature of 800°C for 6 hours, and obtain amorphous carbon after cooling; then calcinate the amorphous carbon in a nitrogen atmosphere at a temperature of 2800°C 4h, naturally cooled to room temperature to obtain graphitized carbon; then graphitized carbon and polypyrrole were dispersed in absolute ethanol at a mass ratio of 1:1, and sprayed into balls after 0.5h of ultrasonic dispersion and 2h of magnetic stirring, wherein , the inlet temperature of the spray into balls is about 190°C, the outlet temperature is about 130°C, and then the precursor is collected by a cyclone separator; next, the precursor is carbonized for 2 hours at a temperature of 1000°C in a nitrogen atmosphere, and porous graphite is obtained after cooling carbonization; finally, 5 g of porous graphitized carbon and 1.2 g of citric acid were dispersed in 60 mL of deionized water, transferred to a wat...
PUM
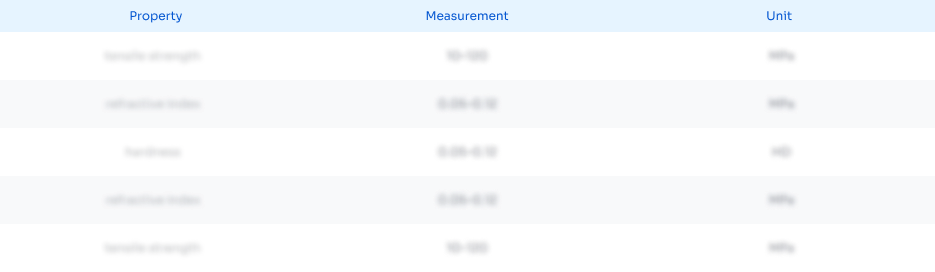
Abstract
Description
Claims
Application Information

- R&D
- Intellectual Property
- Life Sciences
- Materials
- Tech Scout
- Unparalleled Data Quality
- Higher Quality Content
- 60% Fewer Hallucinations
Browse by: Latest US Patents, China's latest patents, Technical Efficacy Thesaurus, Application Domain, Technology Topic, Popular Technical Reports.
© 2025 PatSnap. All rights reserved.Legal|Privacy policy|Modern Slavery Act Transparency Statement|Sitemap|About US| Contact US: help@patsnap.com