Preparation method of Magneli phase low valence titanium oxide
A technology of oxide and low-valent titanium, which is applied in the field of preparation of Magnéli phase low-valent titanium oxide materials, can solve the problems of high cost of Magnéli phase materials, harsh reaction conditions, and high calcination temperature, and achieve the effect of saving production costs
- Summary
- Abstract
- Description
- Claims
- Application Information
AI Technical Summary
Problems solved by technology
Method used
Image
Examples
Embodiment 1
[0041] The mass percentage of the main raw materials aluminum powder and titanium dioxide used in the implementation of Example 1 is: 0.56:1.
[0042] S101: Weigh 50 g of titanium dioxide and 28 g of aluminum powder, add 25 mL of absolute ethanol, mill the weighed titanium dioxide, aluminum powder, and absolute ethanol in a planetary ball mill for 1 hour, and mix well.
[0043] S102: Put the raw material mixed in S101 into the crucible for compaction, and cover the surface of the raw material with a layer of molten B 2 o 3 , a thickness of 3mm, to isolate the air.
[0044] S103: Prepare three identical samples according to the steps of S101 and S102, which are samples a, b, and c respectively.
[0045]S104: Put the samples prepared in S103 into a box-type resistance furnace for roasting, the roasting temperature is 950°C, and the roasting time is 20 min, 25 min, and 30 min respectively, and naturally cool in the air atmosphere after the reaction is completed.
[0046] The m...
Embodiment 2
[0054] The mass percentage of the main raw materials aluminum powder and titanium dioxide used in the implementation of Example 2 is: 0.56:1.
[0055] S101: Weigh 50 g of titanium dioxide and 28 g of aluminum powder, add 30 mL of absolute ethanol, mill the weighed titanium dioxide, aluminum powder, and absolute ethanol in a planetary ball mill for 1 hour, and mix well.
[0056] S102: Put the raw material mixed in S101 into the crucible for compaction, and cover the surface of the raw material with a layer of molten B 2 o 3 , a thickness of 4mm, to isolate the air.
[0057] S103: Put the crucible prepared in S102 into a box-type resistance furnace for calcination, the calcination temperature is 850° C., and the calcination time is 30 minutes. After the reaction is completed, it is naturally cooled in an air atmosphere.
[0058] S104: leaching the prepared material in hydrochloric acid with a concentration of 15%, the leaching time is 10 min, and the stirring speed is 60 rpm. ...
Embodiment 3
[0061] The mass percentage of the main raw materials aluminum powder and titanium dioxide used in the implementation of Example 3 is: 0.68:1.
[0062] S101: Weigh 50 g of titanium dioxide and 34 g of aluminum powder, add 30 mL of absolute ethanol, mill the weighed titanium dioxide, aluminum powder, and absolute ethanol in a planetary ball mill for 1 hour, and mix well.
[0063] S102: Put the raw material mixed in S101 into the crucible for compaction, and cover the surface of the raw material with a layer of molten B 2 o 3 , a thickness of 5mm, to isolate the air.
[0064] S103: Put the crucible prepared in S102 into a box-type resistance furnace for calcination, the calcination temperature is 1000° C., and the calcination time is 10 minutes. After the reaction is completed, cool naturally in the air atmosphere.
[0065] S104: leaching the prepared material in dilute sulfuric acid with a concentration of 20%, for 10 minutes, and at a stirring rate of 60 rpm.
[0066] Implem...
PUM
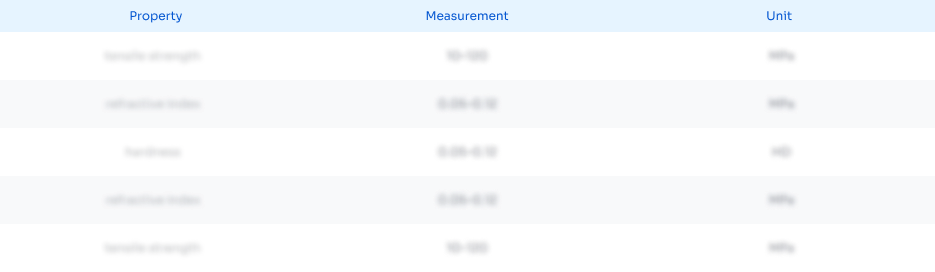
Abstract
Description
Claims
Application Information

- R&D Engineer
- R&D Manager
- IP Professional
- Industry Leading Data Capabilities
- Powerful AI technology
- Patent DNA Extraction
Browse by: Latest US Patents, China's latest patents, Technical Efficacy Thesaurus, Application Domain, Technology Topic, Popular Technical Reports.
© 2024 PatSnap. All rights reserved.Legal|Privacy policy|Modern Slavery Act Transparency Statement|Sitemap|About US| Contact US: help@patsnap.com