Method and device for preparing coating on basis of laser processing technology
A laser processing and technology technology, applied in the field of parts remanufacturing, which can solve the problems of large size disparity of sprayed particles, large amount of element burning loss, uneven coating texture, etc., and achieves accurate and controllable heating temperature, large flexibility, and control of roughness. Effect
- Summary
- Abstract
- Description
- Claims
- Application Information
AI Technical Summary
Problems solved by technology
Method used
Image
Examples
Embodiment Construction
[0033] The device of the present invention includes a laser generator 1, a light guiding and focusing system, a control system, a gas storage system, a water spray system, a workpiece clamping system and a wire feeding system. Wherein said light guiding and focusing system comprises total reflection mirror 6, focusing lens 33, base 39, upper fixed plate 32, stud 41, stud 29 with shoulder, the first thin nut 30, the second Thin nut 37, second nut 38, third nut 40, first nut 35, third gasket 31, fourth gasket 34, split nut 36, lead screw 13, motor 27, motor mounting bracket 24, bolt 25 , the second gasket 26 and the motor base 28 . The gas storage system includes a gas storage tank 5 , a gas valve 9 , and an air guide tube 4 . Described sprinkler system is made up of sprinkler head 17, water valve 18 and the water pipe that connects them. The wire feeding system includes a symmetrical wire feeding motor 20 , a speed reducer 19 , a spraying wire 15 , a wire feeding roller 14 an...
PUM
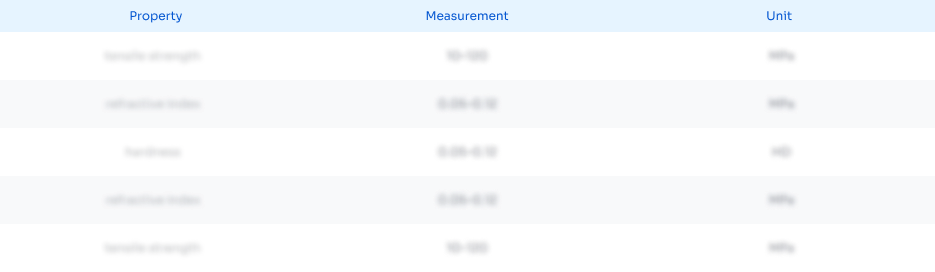
Abstract
Description
Claims
Application Information

- R&D
- Intellectual Property
- Life Sciences
- Materials
- Tech Scout
- Unparalleled Data Quality
- Higher Quality Content
- 60% Fewer Hallucinations
Browse by: Latest US Patents, China's latest patents, Technical Efficacy Thesaurus, Application Domain, Technology Topic, Popular Technical Reports.
© 2025 PatSnap. All rights reserved.Legal|Privacy policy|Modern Slavery Act Transparency Statement|Sitemap|About US| Contact US: help@patsnap.com