Polyvinyl chloride cable material not prone to deformation
A polyvinyl chloride cable and polyvinyl chloride resin technology, which is applied to circuits, electrical components, plastic/resin/wax insulators, etc., can solve the problems of poor heat resistance, poor dimensional stability, and easy deformation, and achieve enhanced heat resistance. , Excellent tear resistance, good heat resistance
- Summary
- Abstract
- Description
- Claims
- Application Information
AI Technical Summary
Problems solved by technology
Method used
Examples
Embodiment 1
[0015] A non-deformable polyvinyl chloride cable material proposed by the present invention, its raw materials include by weight: 20 parts of polyvinyl chloride resin, 25 parts of acrylonitrile-butadiene-styrene copolymer, 30 parts of polypropylene, and 6 parts of polyurethane , 1 part of polypropylene grafted maleic anhydride, 2 parts of vinyl tris(β-methoxyethoxy) silane, 10 parts of modified carbon nanotubes, 3 parts of graphene, 1 part of alumina, 5 parts of silicon carbide , 2 parts of calcium carbonate, 7 parts of talcum powder, 1 part of castor oil, 2 parts of dithiodimorpholine, 2 parts of tert-butyl hydroperoxide, 1.2 parts of methylene bis-o-chloroaniline, poly-p-nitrosobenzene 0.5 parts, 10103 parts of antioxidant, 1 part of chlorinated paraffin, 2 parts of thiodipropionate diester.
Embodiment 2
[0017] A non-deformable polyvinyl chloride cable material proposed by the present invention, its raw materials include by weight: 30 parts of polyvinyl chloride resin, 15 parts of acrylonitrile-butadiene-styrene copolymer, 50 parts of polypropylene, and 2 parts of polyurethane , 2 parts of polypropylene grafted maleic anhydride, 1 part of vinyl tris(β-methoxyethoxy) silane, 20 parts of modified carbon nanotubes, 1 part of graphene, 5 parts of alumina, 1 part of silicon carbide , 8 parts of calcium carbonate, 3 parts of talc, 2 parts of castor oil, 1 part of dithiodimorpholine, 5 parts of tert-butyl hydroperoxide, 0.5 parts of methylenebis-o-chloroaniline, poly-p-nitrosobenzene 1.2 parts, 10101 parts of antioxidant, 2 parts of chlorinated paraffin, 1 part of thiodipropionate diester.
[0018] The modified carbon nanotubes are prepared by the following process: uniformly mix cornstarch, acetic anhydride, and glacial acetic acid to obtain pretreated cornstarch; mix concentrated n...
Embodiment 3
[0020] A non-deformable polyvinyl chloride cable material proposed by the present invention, its raw materials include by weight: 22 parts of polyvinyl chloride resin, 22 parts of acrylonitrile-butadiene-styrene copolymer, 35 parts of polypropylene, and 5 parts of polyurethane , 1.2 parts of polypropylene grafted maleic anhydride, 1.7 parts of vinyl tris(β-methoxyethoxy) silane, 12 parts of modified carbon nanotubes, 2.5 parts of graphene, 2 parts of alumina, 4 parts of silicon carbide , 4 parts of calcium carbonate, 6 parts of talcum powder, 1.2 parts of castor oil, 1.6 parts of dithiodimorpholine, 3 parts of tert-butyl hydroperoxide, 1 part of methylene bis-o-chloroaniline, poly-p-nitrosobenzene 0.6 parts, 10102.5 parts of antioxidant, 1.5 parts of chlorinated paraffin, 1.5 parts of thiodipropionate diester.
[0021] The modified carbon nanotubes were prepared by the following process: mix cornstarch, acetic anhydride, and glacial acetic acid to obtain pretreated cornstarch;...
PUM
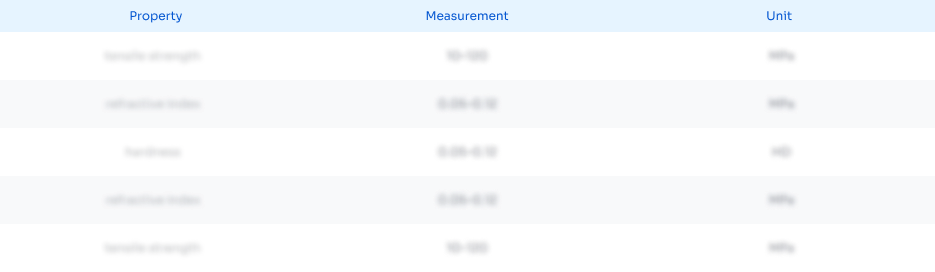
Abstract
Description
Claims
Application Information

- R&D
- Intellectual Property
- Life Sciences
- Materials
- Tech Scout
- Unparalleled Data Quality
- Higher Quality Content
- 60% Fewer Hallucinations
Browse by: Latest US Patents, China's latest patents, Technical Efficacy Thesaurus, Application Domain, Technology Topic, Popular Technical Reports.
© 2025 PatSnap. All rights reserved.Legal|Privacy policy|Modern Slavery Act Transparency Statement|Sitemap|About US| Contact US: help@patsnap.com